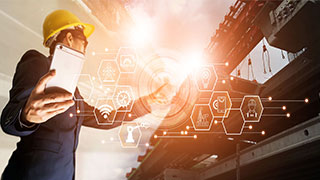
Innovative technologies, processes and products in the construction industry
- Project team:
Christoph Kehl (Project Manager); Matthias Achternbosch; Christoph Revermann
- Thematic area:
- Topic initiative:
Committee on Education, Research and Technology Assessment
- Analytical approach:
TA project
- Startdate:
2019
- Enddate:
2022
Innovations for a more efficient construction industry
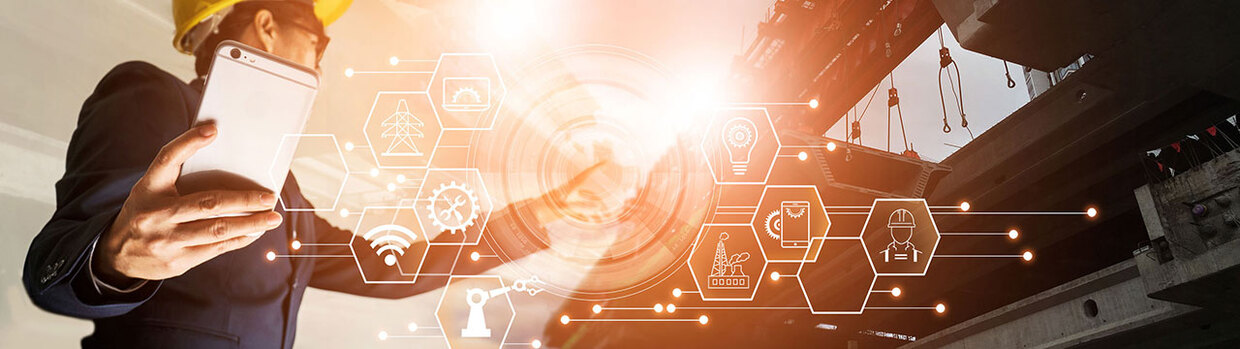
The huge demand for affordable housing represents an enormous national challenge that cannot be met without an efficient and innovative construction industry. The digitisation and automation of construction processes are expected to provide significant impetus for more efficient execution of construction projects. Which (digital) technical innovations are in development, which are being tested or already in use? How can their potential be assessed and what political measures can be taken to overcome the innovation backlog in the industry?
At a glance
sprungmarken_marker_3484
For systemic reasons, the construction industry is one of the weakest sectors in terms of innovation.
The construction industry is one of the very large sectors of the economy. Compared with other sectors, however, it is characterized by relatively low productivity development and low innovation activity (Fig.). The way in which structures are planned and built has remained essentially the same in recent decades. There are systemic reasons for this: In terms of its operational structure, the construction industry is one of the exceptionally fragmented sectors of the economy and is characterized by SMEs that tend to be capital-poor, most of them with fewer than 20 employees, and a large number of very different players (planning offices, craft enterprises, construction companies, building materials manufacturers, etc.). Innovations are therefore often unable to gain widespread acceptance. In addition, there are other factors that inhibit innovation, such as the almost unprecedented standardisation and regulation, as well as the fact that buildings are usually unique and require their own planning and execution.
Digital planning and building offers many efficiency benefits, but implementation in Germany faces hurdles
Although the planning of a building takes place on a computer today, the electronic planning documents are usually still treated like paper documents and exchanged separately. The digital working and planning method BIM provides a remedy. In this process, all the essential information on a structure that is required for planning, construction and subsequent use flows continuously into a digital building model. All relevant project data and planning documents can thus be accessed by all project participants at any time - although this initially entails greater planning effort, it helps to save costs and time throughout the entire process; planning errors can be identified at an early stage and, in particular, cost- and time-intensive retroactive planning changes can be minimized (Fig.). In recent years, the topic of BIM has also gained significant attention in Germany. Nevertheless, BIM implementation lags behind in international comparison, especially in residential construction. Hurdles are the high number of SMEs, which are often deterred by the financially and organisationally costly BIM conversion, as well as the strict separation of planning and execution services, which is also anchored in procurement law.
While prefabricated construction is already established, 3-D concrete printing is still a long way from being implemented on a mass scale
Serial and modular construction also offers obvious opportunities for increasing efficiency and productivity. Buildings are not planned and erected as one-offs, but are either mass-produced in industrial manufacturing processes or assembled from prefabricated components (modules) according to the modular principle. This allows costs to be saved and construction projects to be carried out significantly faster with high precision. In combination with BIM as well as digital and largely fully automated prefabrication methods, unprecedented complexity, variability and precision of prefabricated parts and modules can be achieved today. Additive manufacturing of buildings, colloquially referred to as 3-D printing, on the other hand, still requires longer-term research and development. Although there has been a rapid increase in demonstration projects for 3-D concrete printing of mostly small buildings, both internationally and in Germany, there is still a long way to go. However, the integration of reinforcement as well as the development of printable concrete with sufficient dimensional stability (e.g. for ceiling structures) still pose greater challenges.
In view of increasing sustainability requirements, the development of sustainable building material technologies is of central importance
The building materials industry has basically stuck to the existing system of building materials (e.g., brick, concrete, wood and glass) for decades, producing mostly only incremental innovations. Modern buildings are mostly made of conventional concrete at their core, a material produced in large quantities worldwide and based on Portland cement clinker as a mineral binder. Its production is energy-intensive and associated with high CO2 emissions. The high demands placed on structures in terms of sustainability, durability, thermal insulation, etc. are currently practically only achieved by additive, downstream building material technologies (as in the case of thermal insulation, for example). Therefore, the new or further development of resource- and climate-friendly building material technologies (especially novel cement systems) should be an important focus, since mineral materials cannot be completely substituted by wood.
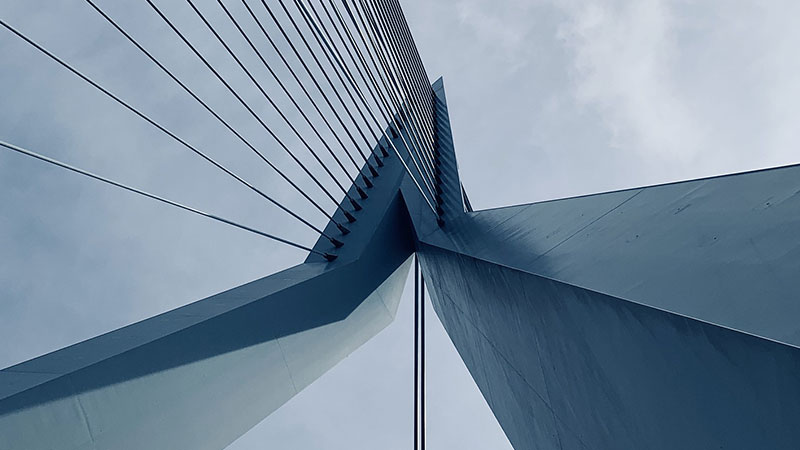
Increasing the innovative capability of the construction industry is at least as much an operational and organisational issue as it is a technological one.
The construction industry is facing a wide range of challenges - increasing productivity and efficiency, rising demands for resource and climate protection with high quality standards - which are unlikely to be mastered without fundamental technological modernisation. However, the promotion of digital technologies alone will not be enough to ensure that innovations are ultimately implemented in practice. What is needed is a much broader perspective that also includes environmental aspects, systemic framework conditions and soft operational aspects (operational management, willingness to take risks, communication culture, etc.). Digitisation requires everyone involved to be prepared to engage in fundamental structural change. Innovations will ultimately only be successful if they meet the requirements and needs of SMEs. These should therefore be involved in innovation and standardisation processes at an early stage.
Downloads
|
TAB-Arbeitsbericht Nr. 199 (only in German) Innovative Technologien, Prozesse und Produkte in der Bauwirtschaft. Endbericht zum TA-Projekt. |
![]() |
|
In the Bundestag
- Vorgang - Bericht, Gutachten, Programm im Dokumentations- und Informationssystem für Parlamentsmaterialien (DIP)