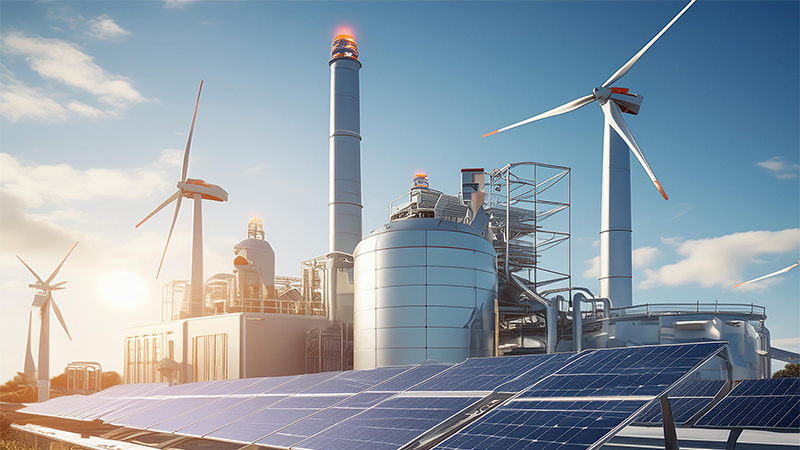
Alternative Technologiepfade für die Emissionsreduktion in der Grundstoffindustrie
- Projektteam:
Claudio Caviezel (Projektleitung),
Matthias Achternbosch, Reinhard Grünwald - Themenfeld:
- Themeninitiative:
Ausschuss für Wirtschaft und Energie
- Analyseansatz:
TA-Projekt
- Starttermin:
2021
- Endtermin:
2023
Die Endberichte zum TA-Projekt wurden vom Ausschuss für Bildung, Forschung und Technikfolgenabschätzung am 15.05.2024 abgenommen und wurden als TAB-Arbeitsberichte Nr. 210 (Ergebnisbericht) und Nr. 211 (Langfassung) am 28.05.2024 veröffentlicht.
Optionen für eine klimaneutrale und nachhaltige Grundstoffindustrie in Deutschland
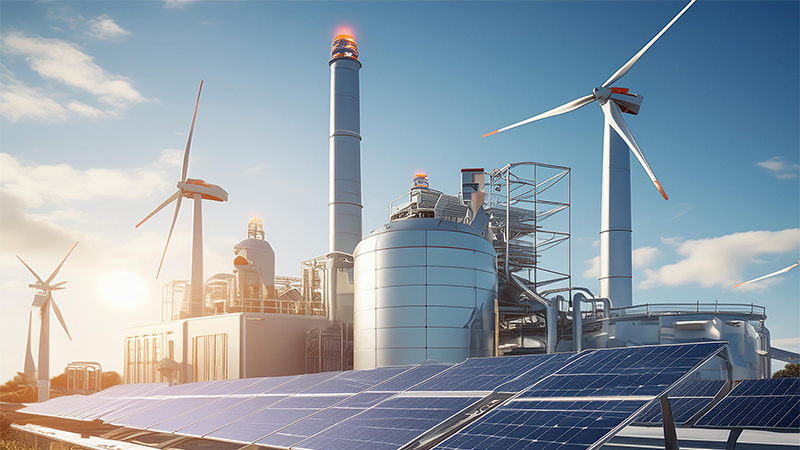
Deutschland soll bis 2045 klimaneutral werden. Das bedeutet, dass auch die Industrie, die 2020 für 176 Mio. t CO2-eq bzw. 24 % der deutschen Treibhausgasemissionen (THG-Emissionen) verantwortlich war, bis 2045 netto keine THG mehr ausstoßen darf. Unter der Maßgabe, dass Industriegüter auch weiterhin in Deutschland in ähnlich hoher Menge wie heute produziert werden sollen, sind innerhalb der nächsten 20 Jahre die konventionellen, überwiegend auf fossilen Ressourcen basierenden Produktionsprozesse auf emissionsarme Verfahren und Rohstoffe umzustellen. Die Transformation ist technisch und wirtschaftlich voraussetzungsreich und für die Industrieunternehmen, die häufig in scharfem internationalem Wettbewerb stehen, auch mit hohen Risiken verbunden.
Bei den Industrieemissionen nimmt die Grundstoffindustrie eine bedeutende Rolle ein, insbesondere die Eisen- und Stahlproduktion (THG-Emissionen 2020: 46 Mio. t CO2-eq), die Zementherstellung (20 Mio. t CO2-eq) sowie die Produktion von organisch-chemischen Grundchemikalien (High-Value-Chemicals – HVC) (8 Mio. t CO2-eq), die gemeinsam für über 40 % der industriellen THG-Emissionen verantwortlich sind. Vor diesem Hintergrund hat der Ausschuss für Bildung, Forschung und Technikfolgenabschätzung des Deutschen Bundestages das Büro für Technikfolgen-Abschätzung beim Deutschen Bundestag (TAB) mit der Durchführung eines TA-Projekts »Alternative Technologiepfade für die Emissionsreduktion in der Grundstoffindustrie« beauftragt. Ziel ist die Analyse der technischen und wirtschaftlichen Realisierungsbedingungen für eine (weitgehende) Klimaneutralität bis 2045 der drei emissionsintensivsten Grundstoffindustrien Eisen/Stahl, Zement und HVC.
Inhalt
sprungmarken_marker_2086
Zielsetzung des TA-Projekts
Auftragsgemäß bestand der Fokus der Untersuchung aus den folgenden vier Aufgabenstellungen, die für jede der drei Grundstoffindustrien behandelt wurden:
- Darstellung der aktuellen (konventionellen) Produktionstechnologien und des Wissensstands zu möglichen Vermeidungstechnologien; Identifizierung technischer und wirtschaftlicher Herausforderungen sowie Ableitung offener Forschungsfragen;
- Modellierung von zwei möglichen Entwicklungspfaden hin zur Klimaneutralität auf Basis der vielversprechendsten Vermeidungstechnologien;
- Diskussion von ökonomischen und die Nachhaltigkeit betreffenden Effekten der Transformation, um Auswirkungen auf Arbeitsplätze, auf vor- und nachgeschaltete Wertschöpfungsketten, auf die Importabhängigkeit sowie Risiken für die Wettbewerbsfähigkeit der deutschen Grundstoffindustrie zu bewerten;
- Ableitung von industrie- und forschungspolitischen Handlungsoptionen zur Beförderung der Transformation hin zu einer klimaneutralen Grundstoffindustrie bis 2045.
Der breite Analyseansatz verweist zugleich auf einige der Herausforderungen, denen sich dieses TA-Projekt zu stellen hatte. Die Untersuchung von drei Grundstoffindustrien, die jede für sich eine hohe Komplexität aufweist und daher einer tiefergehenden Behandlung bedarf, mündete in sehr umfangreichem Analysematerial. Für die Ergebnispräsentation musste eine Darstellungsform gefunden werden, die sowohl die breite (politische) Leserschaft als auch mit dem Thema gut vertraute Personen anzusprechen vermag. Aus diesem Grund wurde der vorliegende komprimierte Ergebnisbericht generiert, der sich in erster Linie an politische Entscheidungsträger/innen und interessierte Laien richtet. In der Langfassung (TAB-Arbeitsbericht Nr. 211), die sich stärker an das Fachpublikum wendet, werden die Methoden und die Analyseergebnisse der TA-Untersuchung detailliert und umfassend dargestellt und erörtert.
Die Durchführung des TA-Projekts fand in einer Zeit statt, die von sehr dynamischen Entwicklungen mit weitreichenden Folgen für die Transformation der Grundstoffindustrie geprägt war. Während der gutachterlichen Arbeit an den Entwicklungspfaden brach der russische Angriffskrieg gegen die Ukraine aus. Seriöse Prognosen zu den mittel- und längerfristigen Auswirkungen des Kriegs auf die ökonomische Entwicklung, die Produktnachfrage, die Rohstoffverfügbarkeiten oder die Preise für Energieträger waren während des Bearbeitungszeitraums (September 2021 bis September 2022) des im Rahmen des Projekts vergebenen Gutachtens (siehe folgenden Abschnitt) nicht möglich. Um die Auswirkungen des Kriegs auf mögliche Entwicklungspfade trotzdem in angemessener Weise berücksichtigen zu können, wurde auf die (vor Kriegsbeginn favorisierte) Rolle von Erdgas als Brückentechnologie zu einer Wasserstoffwirtschaft verzichtet.
Kurz vor Abschluss des TA-Projekts erging schließlich das Urteil des Bundesverfassungsgerichts1 vom 15. November 2023 zum Zweiten Nachtragshaushaltsgesetz 20212, das auch weitreichende Folgen für die Finanzierung von Unterstützungsmaßnahmen für die Transformation der Grundstoffindustrie hat. Die (noch nicht zu überblickenden) Konsequenzen des Urteils konnten in diesem TA-Projekt nicht mehr antizipiert und berücksichtig werden.
Gutachtenvergabe
Im Rahmen des TA-Projekts wurde ein Gutachten vergeben, dessen Ergebnisse neben substanziellen eigenen Recherchen und Analysen in die Berichtserstellung maßgebend eingeflossen sind:
Optionen für eine klimaneutrale und nachhaltige Grundstoffindustrie in Deutschland – Entwicklungspfade für ausgewählte Wirtschaftszweige. Dr. Alexander Piégsa; Dr. Fabian Muralter; Paurnima Kulkarni; Jan Limbers; Sebastian Lübbers, Dr. Almut Kirchner; Dr. Sascha Samadi; Prognos AG in Zusammenarbeit mit dem Wuppertal Institut, BaselGU
Die Verantwortung für die Auswahl, Strukturierung und Verdichtung des Materials sowie dessen Zusammenführung mit Informationen aus eigenen Recherchen und Analysen liegt bei den Bearbeitern, Dr. Claudio Caviezel, Dr. Matthias Achternbosch und Dr. Reinhard Grünwald. Den Gutachter/innen sowie allen an der Erstellung des Gutachtens wie auch des TAB-Berichts beteiligten Expert/innen sei für ihre engagierte Kooperation und ihre Diskussionsbereitschaft herzlich gedankt.
Aufbau des Ergebnisberichts
Der Ergebnisbericht ist wie folgt aufgebaut.
Kapitel 2 enthält für die drei ausgewählten Grundstoffindustrien Eisen/Stahl, Zement und HVC eine Kurzdarstellung des Status quo zu Herstellungsverfahren und THG-Emissionen an den heutigen Produktionsstätten. Für mögliche Vermeidungstechnologien werden jeweils der Stand der Technik und das THG-Reduktionspotenzial abgeschätzt sowie Perspektiven und noch zu bewältigende Herausforderungen herausgearbeitet.
Kapitel 3 stellt die Ergebnisse der Modellierung von zwei möglichen Entwicklungspfaden der Transformation vor, die sich maßgeblich im Grad der internationalen Kooperation unterscheiden. Neben einem Vergleich des Gesamtenergiebedarfs werden auch ökonomische Kennzahlen quantitativ abgeschätzt.
In Kapitel 4 werden ökologische und die Nachhaltigkeit betreffende Effekte der Transformation, aber auch sozioökonomische und standortpolitische Auswirkungen werden mithilfe qualitativer Analysen und Plausibilitätsüberlegungen behandelt.
In Kapitel 5 schließlich werden zum einen politische Handlungsoptionen zur Förderung der Transformation vorgestellt und zum anderen offene technologische Forschungs- und Entwicklungsfragen präsentiert.
Im Ergebnisbericht wurde auf Quellenangaben verzichtet, diesbezüglich wird auf die Langfassung verwiesen.
2 Status quo und Vermeidungstechnologien
Den Ausgangspunkt für die Transformation der Grundstoffindustrien bilden die heutigen Produktionsstätten. Die hier angewandten, überwiegend auf fossilen Ressourcen basierenden Produktionsverfahren müssen auf neue, klimafreundliche Herstellungsprozesse umgestellt werden.
2.1 Eisen- und Stahlerzeugung
Die derzeit 16 deutschen Hochöfen produzieren im Mittel 30 Mio. t Rohstahl pro Jahr. Hinzu kommen noch ca. 1 Mio. t Rohstahl aus dem methanbasierten Direktreduktionsverfahren in Hamburg sowie ca. 12 Mio. t an Sekundärstahl durch Einschmelzen von Eisen- und Stahlschrott. Die Produktionsmenge blieb während der letzten zwei Dekaden weitgehend stabil (historischer Trend 1995–2019: -0,12 %/Jahr), abgesehen von zwei kurzen Einbrüchen 2009 nach der Finanzkrise und 2020 während der Pandemie.
2.1.1 Konventionelle Produktionsverfahren
In der konventionellen Hochofenroute wird Eisenerz (Eisenoxid – Fe2O3) unter Einsatz von Kohle zu Roheisen (Fe) reduziert. Das dabei gebildete CO2 ist für den Löwenanteil der THG-Emissionen der Stahlherstellung verantwortlich. Im Hochofen entstehen flüssiges Roheisen und als Nebenprodukt Schlacke, die im Erz mitgeführte Minerale und Gesteinsreste (als Gangart bezeichnet) enthält. Das flüssige Roheisen wird im Konverter zu Stahl weiterverarbeitet. Dazu wird Sauerstoff eingeblasen, um den Kohlenstoffgehalt einzustellen und Verunreinigungen zu entfernen. Durch Zusatz weiterer Stoffe, wie Mangan oder Nickel, werden die Eigenschaften des Stahls bestimmt. Heute sind über tausend verschiedene Stahlsorten normiert.
Beim methanbasierten Direktreduktionsverfahren wird Erdgas anstelle von Kohle als Reduktionsmittel verwendet. Dadurch lässt sich der Brennstoffbedarf und damit der CO2-Ausstoß pro t Roheisen reduzieren. Es entsteht ein fester Eisenschwamm3, der für die Weiterverarbeitung eingeschmolzen werden muss.
In der Elektrostahlroute der Sekundärstahlproduktion wird Eisen- und Stahlschrott in einem Elektrolichtbogenofen (Electric Arc Furnace – EAF) aufgeschmolzen. Der Energiebedarf wird hier in erster Linie durch Strom gedeckt. Kohlenstoff wird als zusätzlicher Energielieferant, Schäumungsmittel und für die Einstellung des Kohlenstoffgehalts im Stahl benötigt.
Die gesamten THG-Emissionen der Stahlherstellung (inklusive der vorbereitenden Schritte wie Kokerei und des Walzwerks) betrugen rd. 55 Mio. t CO2-eq/Jahr während der letzten beiden Dekaden (ohne die krisenbedingten Einbrüche 2009 und 2020). Mit einem Anteil von fast 95 % an den Gesamtemissionen dominierte die Hochofenroute, während die Elektrostahlroute mit 1,6 % nur geringfügig beitrug (allerdings ohne THG-Emissionen durch Fremdstrombezug, die dem Energiesektor zugerechnet werden).
2.1.2 Vermeidungstechnologien
In diesem TA-Projekt wurden Vermeidungstechnologien behandelt, die den (aktuellen) Rahmenbedingungen der deutschen Stahlwerke angepasst sind. Die drei ausgewählten Technologieoptionen werden in Kapitel 3.1.3 der Langfassung ausführlich erläutert und im Folgendem zusammenfassend dargestellt. Die zugehörigen Prozessketten sind in Abbildung 2.1 schematisch dargestellt.
Abb. 2.1 Ausgewählte alternative Routen der Stahlproduktion mit Prozessschritten und Zwischenprodukten
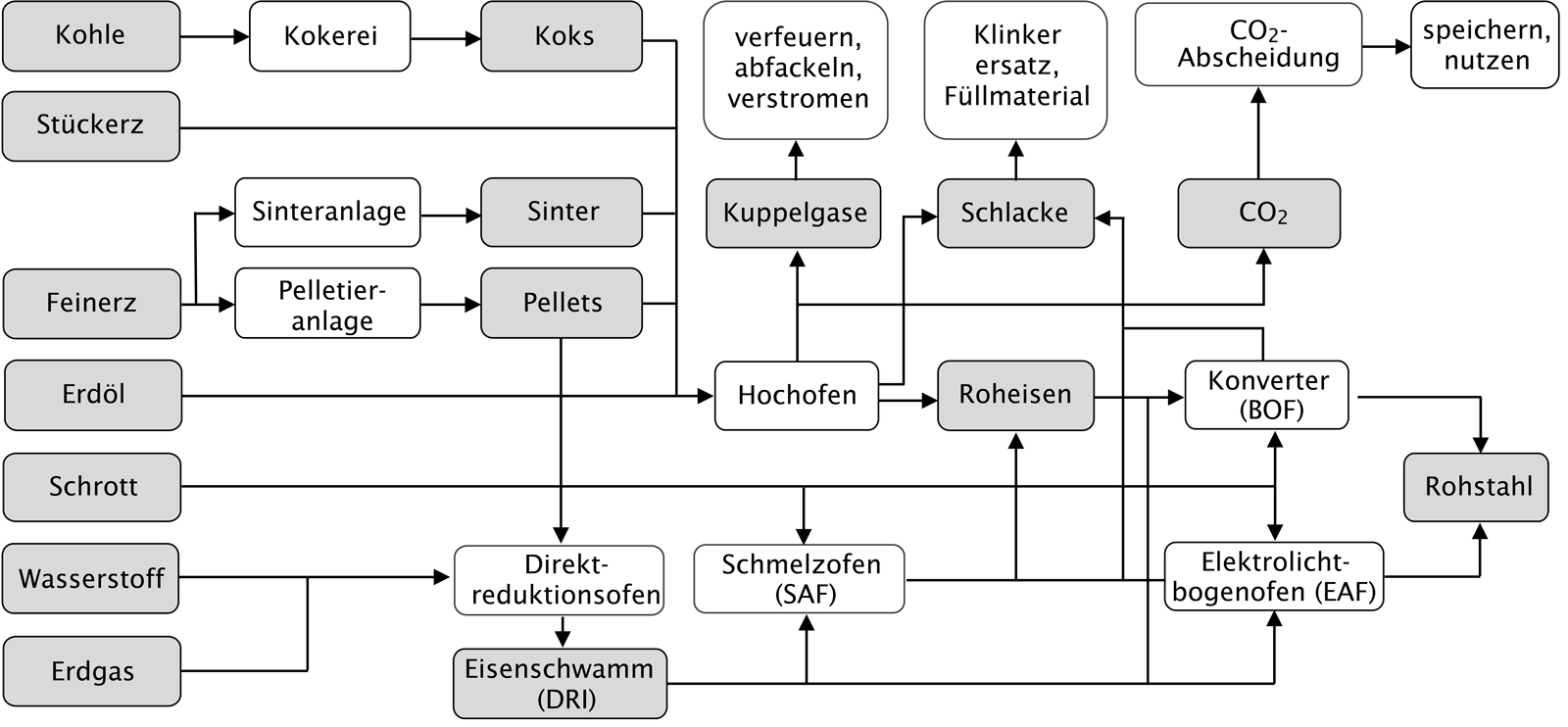
Eigene Darstellung nach Prognos/Wuppertal Institut 2022
H2-Direktreduktion mit Elektrolichtbogenofen (EAF)
In dieser Route wird das Eisenerz im Direktreduktionsofen (DR-Ofen) mithilfe von Wasserstoff (H2) anstelle von Kohle zu Eisenmetall reduziert, wobei kein CO2 entsteht. Um ein Zuwachsen des Ofens zu vermeiden, wird das Eisen nicht geschmolzen. Es entsteht ein fester Eisenschwamm[3], der die im Erz mitgeführte mineralische Gangart noch enthält. In einem zweiten Schritt wird der Eisenschwamm im EAF gemeinsam mit Eisen- und Stahlschrott aufgeschmolzen und zu Stahl verarbeitet. Die im Eisenschwamm noch enthalte Gangart muss im EAF über eine Schlacke abgetrennt werden, was den elektrischen Energiebedarf erhöht. Daher werden hochwertige, d. h. gangartarme Eisenerze favorisiert, die aber nur in begrenzter Menge und zu höheren Preisen verfügbar sind.
Das DR-Verfahren wird bislang großtechnisch mit einem Gemisch aus Erdgas und Wasserstoff eingesetzt (z. B. in Hamburg). Mitte 2023 wurde in Lingen die weltweit größte reine H2-DR-Pilotanlage eröffnet, die industrielle Reife von H2-DR-Öfen wird noch vor 2030 erwartet. Eine Herausforderung für diese Route stellen eventuell im Eisenschwamm vorhandene Störstoffe (wie Stickstoff oder Schwefel) dar, die im EAF nicht abgetrennt werden können und daher eine aufwändige Nachbehandlung erfordern. Eine weitere Schwierigkeit ist der gegenüber Konvertern geringere Durchsatz von EAF, wodurch Anpassungen in den nachfolgenden Aggregaten und der Stahlwerkslogistik nötig werden könnten.
Sofern grüner Wasserstoff verwendet wird, kann Eisenschwamm nahezu emissionsfrei hergestellt werden. Geringe unvermeidbare CO2-Emissionen entstehen durch den notwendigen Kohlenstoff im EAF. Wird der EAF mit erneuerbarem Strom betrieben, beträgt das THG-Reduktionspotenzial gegenüber der konventionellen Hochofenroute bis zu 96 %.
Der Technologiewechsel ist mit hohen Kosten verbunden, da komplett neue Anlagen erforderlich sind. Die Investitionskosten pro t Rohstahl übersteigen diejenigen eines Retrofits aller Anlagenteile der konventionellen Hochofenroute um mehr als das Zweifache (bei Eigenerzeugung des benötigten Wasserstoffs mittels Elektrolyse um mehr als das Fünffache). Die Investitionskosten dürften in den kommenden Jahren allerdings sinken. Für die operativen Kosten kann anfangs eine Steigerung von über 50 % gegenüber der konventionellen Stahlproduktion angenommen werden.
H2-Direktreduktion mit Schmelzofen (SAF) und Konverter
In dieser Route wird Eisenerz ebenfalls mittels H2 im DR-Ofen zu Eisenschwamm reduziert. Dieser wird jedoch in einem elektrischen Schmelzofen (Submerged Arc Furnace – SAF) verflüssigt und von der Gangart befreit. Das flüssige Roheisen wird schließlich im konventionellen Konverter zu Stahl weiterverarbeitet. Gegenüber dem Einsatz des EAF hat diese Route eine Reihe von Vorteilen: Weil die Stoffflüsse des SAF auf die Abstichmenge der vormaligen Hochöfen abgestimmt werden können, bleiben im Stahlwerk vorhandene Konverter und nachfolgende Aggregate weiterhin nutzbar. Der SAF kann auch gangartreicheres DRI verarbeiten, sodass weniger hohe Ansprüche an die Qualität des Eisenerzes gestellt werden. Weil die konventionelle Konvertermetallurgie bestehen bleibt, können weiterhin alle Stahlqualitäten hergestellt werden.
Elektrische Schmelzöfen zur Herstellung von reinem Roheisen sind noch nicht im industriellen Maßstab verfügbar, das Verfahren muss also noch erprobt werden. Eine Herausforderung stellt die Energiezufuhr für den Konverter dar: In der konventionellen Hochofenroute dient der im Roheisen enthaltene Kohlenstoff als Energielieferant im Konverter. Wasserstoffreduzierter Eisenschwamm enthält aber keinen Kohlenstoff, sodass dieser im SAF zugegeben werden muss. Zusammen mit Anlagenbauern entwickelt beispielweise Thyssenkrupp eine strombasierte Schmelzeinheit, um seine Stahlproduktion in Duisburg schrittweise auf diese Route umzustellen.
Das THG-Einsparpotenzial dieser Route wird gegenüber der konventionellen Hochofenroute auf 95 % geschätzt (bei Verwendung von grünem Wasserstoff für den DR-Ofen und erneuerbarem Strom für den SAF).
Die Investitionskosten für einen Technologiewechsel übersteigen diejenigen eines Retrofits für die konventionelle Hochofenroute um mehr als das Dreifache (bei Eigenerzeugung des benötigten Wasserstoffs mittels Elektrolyse um mehr als das Sechsfache). Bei den operativen Kosten kann anfangs eine Steigerung von über 60 % angenommen werden.
Hochofen mit Konverter und CO2-Abscheidung
Bei dieser Option wird die konventionelle Hochofenroute um Anlagen für die CO2-Abscheidung erweitert, an den eigentlichen Prozessen der Eisen- und Stahlerzeugung ändert sich nichts. Idealerweise müsste sich die CO2-Abscheidung auf alle Komponenten der Stahlerzeugung (u. a. Kokerei, Hochofen, Konverter, Walzwerk, Gichtgaskraftwerk) erstrecken, allerdings limitieren die schieren Ausmaße eines Stahlwerks die praktische Umsetzbarkeit auf den Hochofen. Erwartet wird so eine Abscheidungsrate von ca. 50 % der THG-Emissionen der Hochofenroute.
Noch ist keine CO2-Abscheidung an einem konventionellen Stahlwerk industriell umgesetzt, erste Demonstrationsprojekte laufen derzeit an. So zielt etwa das von Thyssenkrupp lancierte Projekt »Carbon2Chem« darauf ab, CO2 aus der Stahlindustrie als Ausgangsstoff für die Chemieindustrie zu nutzen. Aus verfahrenstechnischer Sicht ist die Nachrüstung im Vergleich zu anderen Vermeidungsoptionen deutlich einfacher und kostengünstiger umzusetzen. Die Nachrüstung im Rahmen eines Retrofits würde zu Investitionsmehrkosten von ca. 70 % führen und auch die operativen Kosten würden durch den zusätzlichen Strombedarf für die CO2-Abscheidung nur marginal erhöht.
2.2 Zement
In Deutschland produzieren 54 Werke ca. 35,5 Mio. t Zement im Jahr. Davon sind 19 reine Mahlwerke (ohne eigene Klinkererzeugung, d. h. ohne Ofenanlagen), in denen Zemente aus Klinker und weiteren Zumahlstoffen gemahlen und gemischt werden.
2.2.1 Konventionelle Produktionsverfahren
Die Herstellung von Zement erfolgt in zwei Stufen. Im ersten Schritt wird ein Rohstoffgemisch aus feingemahlenem Kalkstein und Ton bei Temperaturen von 1.450 °C zu Portlandzementklinker (auch Zementklinker oder nur Klinker genannt) gebrannt. Dabei wird im Kalkstein gebundenes CO2 abgespalten. Diese Prozessemissionen sind für etwa zwei Drittel der Gesamtemissionen der Zementherstellung verantwortlich, der Rest entsteht durch fossile Brennstoffe für den Ofenbetrieb.
Im zweiten Schritt wird Klinker zusammen mit Zumahlstoffen wie Kalkstein, Hüttensand, Flugasche und Gips zu Zement gemahlen. Die Zusammensetzung der Bestandteile bestimmt die betontechnischen Eigenschaften (z. B. Festigkeit, Erstarrungsverhalten, Dauerhaftigkeit) und damit die Anwendungsbereiche (z. B. Standardhochbau, konstruktiver Tiefbau) der Zemente. Normen legen Zusammensetzung, Anforderungen und Anwendungsbereiche für ein Portfolio an Normzementen fest.
Die THG-Emissionen der deutschen Zementwerke betragen derzeit in der Summe rund 20 Mio. t CO2-eq/Jahr. Die Höhe der Emissionen hat sich innerhalb der letzten Dekade kaum verändert.
2.2.2 Vermeidungstechnologien
Das Ziel einer (weitgehend) klimaneutralen Zementindustrie bis 2045 erfordert aus heutiger Sicht zwingend den Einsatz von CO2-Abscheidung und -Speicherung (CCS) bzw. -Nutzung (CCU). Durch weitere Optionen kann der Bedarf an CO2-Abscheidung verringert werden. Die Vermeidungstechnologien werden in Kapitel 3.2.3 der Langfassung detailliert erläutert. Die Abbildung 2.2 dient als Orientierung im Geflecht der Prozessschritte bei der Zementherstellung.
Abb. 2.2 Routen der Zementproduktion mit Prozessschritten und Zwischenprodukten (vereinfachte Darstellung)
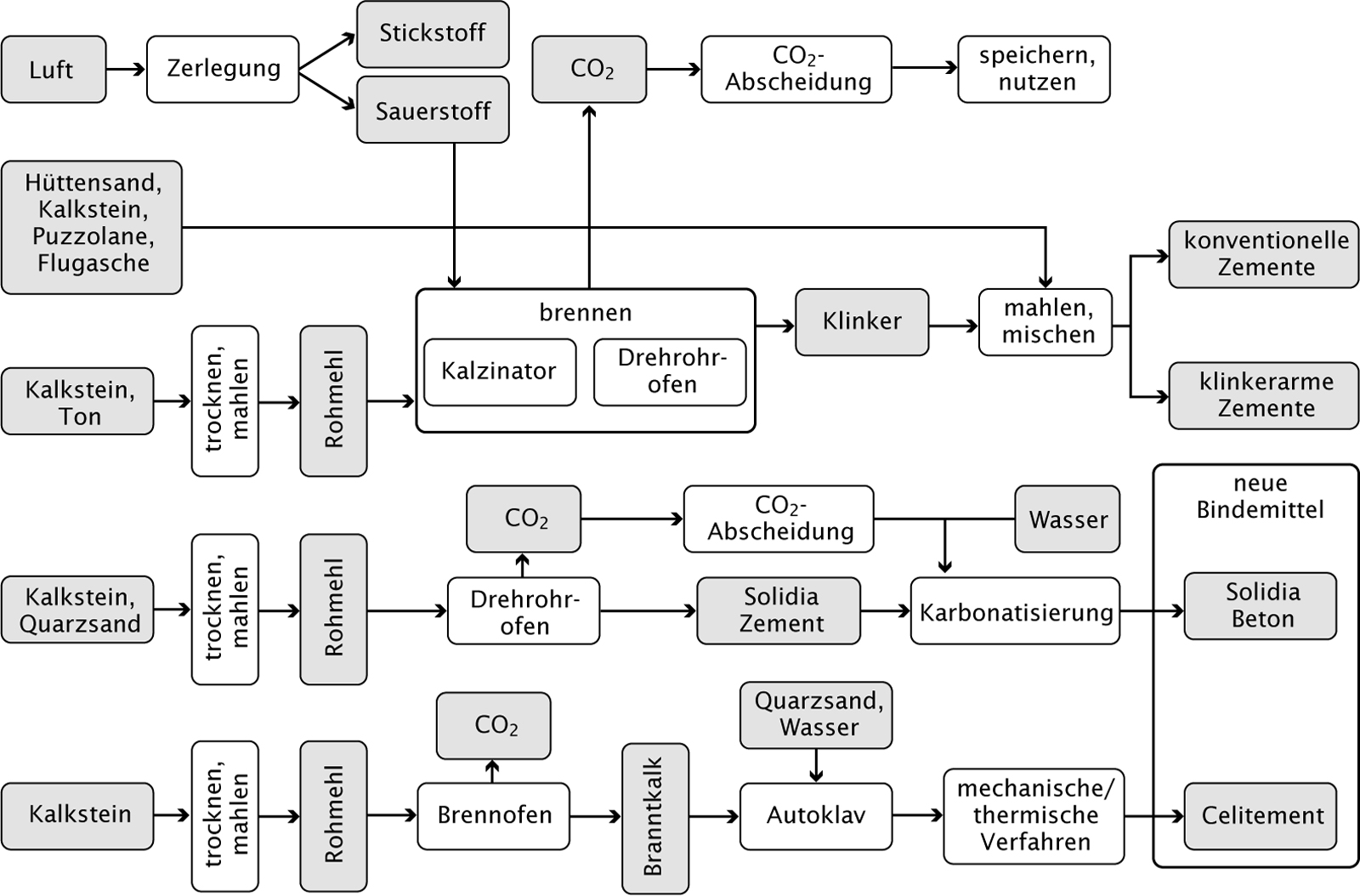
Eigene Darstellung nach Prognos/Wuppertal Institut 2022
Einsatz neuer klinkerarmer Normzemente
Bei der Klinkerherstellung entsteht unvermeidbar CO2. Eine Strategie zur CO2-Reduktion besteht daher in der Absenkung des Klinkeranteils im Zement. Die Entwicklung und Erprobung klinkerarmer Zemente wurde in der letzten Dekade durch den Verein Deutscher Zementwerke (VDZ) vorangetrieben. Seit 2021 sind neue Zementarten genormt, die gegenüber den am Markt etablierten Portlandkompositzementen den Klinkeranteil bis auf 35 % senken können (zum Vergleich: herkömmliche Portlandkompositzemente weisen einen Klinkeranteil von mind. 65 % auf). Ziel ist es, den über alle Zementarten gemittelten Klinkerfaktor bis 2045 auf einen Wert zwischen 53 und 63 % zu senken (heute: 71 %).
Der fehlende Klinker muss durch größere Anteile an Zumahlstoffen ersetzt werden, was die Zusammensetzung der klinkerarmen Zemente komplexer macht. Außerdem hängen die betontechnischen Eigenschaften (und damit die Anwendungsbereiche) in immer stärkerem Maße von der Leistungsfähigkeit der verwendeten Zumahlstoffe ab. Allerdings zeichnet sich bei hochwertigen Zumahlstoffen, wie Hüttensand (infolge der Transformation der Stahlindustrie) oder Flugasche (infolge des Ausstiegs aus der Kohleverstromung), für die Zukunft ein Mangel ab (Kap. 7.2.4 der Langfassung). Große Hoffnungen werden daher auf neue Zumahlstoffe wie Tonminerale gesetzt. An der Normierung und Einführung entsprechender Zemente wird derzeit gearbeitet. In Bezug auf ihre Leistungsfähigkeit und die Realisierungsbedingungen für einen Masseneinsatz bestehen allerdings noch offene Fragen.
Das THG-Reduktionspotenzial klinkerarmer Zemente lässt sich derzeit nur anhand von Modellrechnungen abschätzen (Kap. 3.2.3.1 der Langfassung). Demnach lassen sich gegenüber einem Referenzzement mit Bezugsjahr 2020 in Abhängigkeit von der Zementart die prozessbedingten THG-Emissionen bis 2045 um 30 bis 44 % und die brennstoffbedingten um 26 bis 42 % reduzieren.
Die weitere Preisentwicklung für Zement ist infolge der Auswirkungen des Ukrainekriegs auf die Rohstoff- und Energiepreise nur schwer abschätzbar. Vermutlich wird das Preisniveau der neuen klinkerarmen Zemente aber mit jenem der konventionellen Zemente vergleichbar sein.
Einsatz neuer Bindemittelsysteme
An neuen emissionsarmen Bindemitteln als Alternative zu den klinkerbasierten Systemen wird schon seit Jahrzehnten gearbeitet. Die Herausforderung besteht darin, eine niedrige CO2-Intensität mit einer hohen Leitungsfähigkeit zu verbinden. Als vielversprechende Ansätze wurden in diesem TA-Projekt neue calciumhaltige Bindemittelsysteme identifiziert. Bekannte Vertreter dieser Bindemittelgruppe sind z. B. Celitement oder Solidia. Das dem Celitement zugrundeliegende Bindemittel ist besonders calciumarm und somit weniger emissionsintensiv in der Herstellung, hat aber gleichzeitig ein hohes Potenzial für eine breitere Anwendung. Solidia basiert auf der Idee, dass das bei der Herstellung freigesetzte CO2 direkt wieder aufgenommen wird. Dazu findet das Aushärten in einer CO2-Atmosphäre statt, weshalb sich dieses Verfahren vorrangig für Fertigteile im seriellen Bauen eignet. Für Celitement und Solidia existieren bereits erste Herstellungsanlagen im Industrie- oder zumindest Pilotmaßstab. Vor Eintritt in den Massenmarkt müssen die Bindemittel aus Sicherheits- und Gewährleistungsgründen aufwendig getestet und genormt werden, was typischerweise 15 Jahre und mehr beansprucht. Aus diesem Grund werden bis 2045 nur geringe Marktanteile zwischen 5 bis 10 % erwartet.
Das THG-Reduktionspotenzial von Celitement ist vom eingestellten Calciumgehalt abhängig. In diesem TA-Projekt wurden die Einsparungen gegenüber einem Referenzzement mit Bezugsjahr 2020 auf ca. 13 % bei den Prozessemissionen und 11 % bei den brennstoffbedingten Emissionen geschätzt. Für Solidia werden eine rohstoffliche CO2-Reduktion von ca. 78 % und eine brennstoffliche von 10 % erwartet.
Einsatz der CO2-Abscheidung – Oxyfuel CCS/CCU
Der Beitrag durch klinkerarme Normzemente und neue Bindemittelsysteme wird aus heutiger Sicht nicht ausreichen, um bis 2045 Klimaneutralität in der Zementindustrie zu erreichen. Verbleibende CO2-Emissionen müssen daher abgeschieden und gespeichert werden. Als dafür geeignetes Verfahren gilt die Oxyfuel-CCS-Technologie. Statt Umgebungsluft wird Sauerstoff im Klinkerbrennprozess verwendet, wodurch CO2 im Abgasstrom in hoher Konzentration anfällt und sich daher gut abscheiden lässt. Das CO2 wird gereinigt, verflüssigt und über ein Leitungssystems abtransportiert. Aus heutiger Sicht käme etwa eine CO2-Speicherung in der Nordsee vor der norwegischen Küste infrage, dazu müsste jedoch ein entsprechendes Pipelinesystem realisiert werden.
Für die Umsetzung der Oxyfuel-CCS-Technologie sind neben der CO2-Abscheidung auch für die Verbrennung ofentechnisch Nachrüstungen notwendig. Die Marktreife wird zwischen 2025 und 2030 erwartet. Die Integration der Oxyfuel-CCS-Technologie führt zu einem wesentlich höheren Strombedarf für die Klinkerherstellung, was sich auch in höheren Betriebskosten niederschlägt.
2.3 HVC
Unter HVC werden organisch-chemische Grundchemikalien verstanden, die in verschiedenen Produktionsrouten zu Kunststoffen, Waschmitteln, Lacken, Kühlmitteln, Weichmachern und anderen chemischen Endprodukten weiterverarbeitet werden. Unterschieden wird zwischen den Olefinen (Ethylen, Propylen und Butadien) sowie den Aromaten (Benzol, Toluol und Xylol – BTX-Aromaten). In Deutschland werden derzeit über 13 Mio. t HVC/Jahr produziert, davon rund 80 % Olefine und 20 % Aromaten.
2.3.1 Konventionelle Produktionsverfahren
Die Herstellung von HVC erfolgt bisher fast ausschließlich auf der Basis von Erdölfraktionen durch Steamcracken oder durch Reformieren in petrochemischen Raffinerien. Die wichtigste Route in Deutschland ist das Steamcracken: Fossiles Naphtha aus Erdöl wird in einem Rohrreaktor für wenige Sekunden Temperaturen von ca. 800 °C ausgesetzt und dabei in die verschiedenen HVC gespalten. In Deutschland werden aktuell 13 Steamcracker an 6 Chemiestandorten betrieben. Hier ist die HVC-Produktion in weitere chemische Produktionsprozesse eingebunden, wodurch ein hochkomplexes Gefüge entsteht, das in seinen optimierten Massen- und Energieströmen sowie wirtschaftlichen Verflechtungen schwer zu überschauen ist.
Die prozessbedingten THG-Emissionen der HVC-Produktion belaufen sich aktuell auf 8 Mio. t CO2-eq/Jahr. Hinzu kommen rohstoffbedingte THG-Emissionen durch die Gewinnung von Rohöl und die Herstellung von fossilem Naphtha, die aktuell auf rd. 11 Mio. t CO2-eq/Jahr eingeschätzt werden.
2.3.2 Vermeidungstechnologien
Vermeidungstechnologien für die HVC-Produktion zielen auf eine Reduktion der prozesstechnischen oder der rohstoffbedingten THG-Emissionen (bzw. eine Kombination davon) ab. Für Letzteres muss Rohöl bzw. fossiles Naphtha durch emissionsarm hergestellte Kohlenwasserstoffe, z. B. aus Biomasse, Altkunststoffen, abgeschiedenem CO2 und H2 aus der Wasserelektrolyse, substituiert werden. Damit stehen viele verschiedene alternative Produktionsrouten zur Verfügung, was den Untersuchungsgegenstand komplex macht (Abb. 2.3). Es wurden folgende drei alternative Herstellungsrouten untersucht.
E-Cracker
Statt mit fossilen Energieträgern wird der Steamcracker elektrisch betrieben. Dazu müssen die Gasöfen durch elektrisch beheizte Öfen ersetzt werden, die übrige Anlagentechnik kann weiterverwendet werden. Die industrielle Umsetzung der Elektrifizierung wird aktuell nachdrücklich verfolgt und ist für die kommenden Jahre zu erwarten. Durch den Technologiewechsel steigt der Strombedarf um das 10-Fache, während fossile Brennstoffe wegfallen. Bei Verwendung von erneuerbarem Strom lassen sich die prozessbedingten THG-Emissionen vollständig vermeiden.
Wird weiter fossiles Naphtha eingesetzt, bleiben die rohstoffbedingten THG-Emissionen bestehen. Durch einen Wechsel auf synthetisches Naphtha aus CO2 und grünem Wasserstoff bzw. auf Basis von Pyrolyseöl aus dem chemischen Recycling lassen sich auch diese Emissionen praktisch auf null reduzieren. Hierfür sind allerdings große Mengen an erneuerbaren Energien bzw. an Altkunstoffen erforderlich.
Methanol to Olefin (MtO)
Mit dem Methanol-to-Olefin(MtO)-Verfahren können Olefine wie Ethylen und Propylen aus Methanol katalytisch hergestellt werden. Es wurden verschiedene Verfahren entwickelt und zum Teil bereits großtechnisch umgesetzt (vor allem in China, nicht aber in Deutschland). Die notwendige Energie wird elektrisch zugeführt, sodass bei Verwendung von erneuerbarem Strom keine Prozessemissionen anfallen. Als Rohstoff für das MtO-Verfahren werden große Mengen an Methanol benötigt. Dieses kann emissionsfrei über die Synthese von CO2 und grünem Wasserstoff hergestellt werden, die Produktion ist allerdings strom- und kapitalintensiv.
Der Technologiewechsel auf die MtO-Route würde den Bau von Neuanlagen mit entsprechend hohen Investitionskosten erfordern. Außerdem stellen niedrige Methanolpreise eine zentrale Bedingung für eine wirtschaftliche Olefinproduktion über diese Route dar.
Über die Methanolroute sollen künftig auch Aromaten synthetisiert werden. Methanol-to-Aromatics(MtA)-Verfahren werden seit Jahrzehnten erforscht und entwickelt, deren Marktreife ist jedoch geringer als bei den MtO-Verfahren.
Abb. 2.3 Routen der HVC-Produktion (vereinfachte Darstellung)
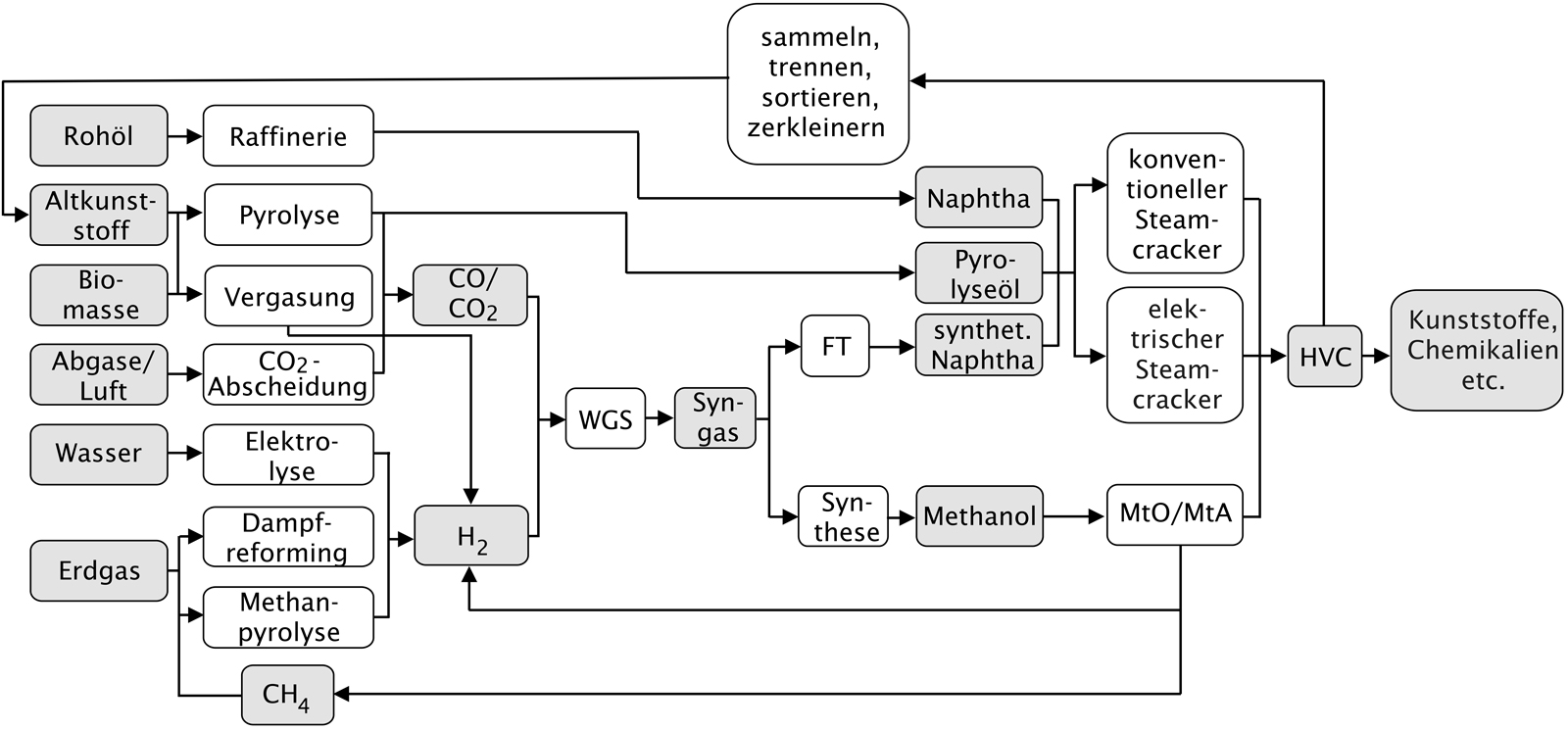
Prozessschritte umrandet, (Zwischen-)Produkte grau unterlegt
Eigene Darstellung nach Prognos/Wuppertal Institut 2022
Chemisches Recycling
Als weitere Option zur Reduktion der rohstoffbedingten THG-Emissionen wurde die Herstellung von Pyrolyseöl aus Kunststoffabfällen untersucht. Die stoffliche Verwertung von Kunststoffabfällen beruht heute weitgehend auf dem mechanischen Recycling, bei dem Altkunststoff gereinigt und direkt wiederverwertet wird. Beim chemischen Recycling werden die Abfälle auf molekularer Ebene in ihre Ausgangsstoffe zerlegt, um sie wieder als Rohstoffe zu verwenden. Dafür wurden verschiedene Verfahren entwickelt. Vor allem Öle aus dem Pyrolyseverfahren weisen ähnliche Eigenschaften wie Naphtha auf, weswegen sie sich gut für die Weiterverarbeitung zu HVC in E-Crackern eignen. Bei der Pyrolyse wird Altkunstoff bei Temperaturen von 300 bis 700 °C unter Sauerstoffausschluss in ein Produktgemisch aufgespalten, das aus festen, flüssigen (Pyrolyseöle) und gasförmigen Anteilen besteht. Der thermische Energiebedarf ist allerdings hoch: Im Vergleich zu fossilem Naphtha resultiert dabei fast eine Verdreifachung des Energieeinsatzes für die Rohstoffbereitstellung, weshalb mit Blick auf die Emissionsbilanz erneuerbare Energien nötig sind.
Am chemischen Recycling von Kunststoffabfällen wird bereits seit den 1980er Jahren geforscht. Allerdings blieb aufgrund technischer und wirtschaftlicher Herausforderungen eine breitere Anwendung bislang aus. Deutlich steigende Preise für fossile Energieträger dürften die Wirtschaftlichkeit des chemischen Recyclings aber begünstigen, sodass für die nächsten Jahre ein starker Markthochlauf erwartet wird. Die Realisierungsbedingungen für diese Route hängen schließlich auch von der Verfügbarkeit von Altplastik ab.
3 Technische Entwicklungspfade für eine klimaneutrale Produktion
Je nach Auswahl der Vermeidungstechnologien und der Umstellungsgeschwindigkeit sind viele mögliche Entwicklungspfade hin zu einer weitgehend klimaneutralen Grundstoffindustrie bis 2045 denkbar. Jeder dieser Pfade ist mit unterschiedlichen Ressourcenbedarfen, Kosten und Auswirkungen, z. B. auf die Bruttowertschöpfung, die Beschäftigung oder die Umwelt, verbunden. Im Rahmen des TA-Projekts wurden für die drei ausgewählten Grundstoffindustrien je zwei mögliche Entwicklungspfade untersucht. Die Konzeption und Modellierung der Pfade erfolgte durch die beauftragten Gutachter/innen von Prognos und Wuppertal Institut.
Für die Modellierungen der Entwicklungspfade und für die Ableitung von ökonomischen Effekten mussten, wie dies bei Szenarien üblich ist, Vereinfachungen und Plausibilitätsannahmen getroffen werden. Gewisse Abweichungen und Inkonsistenzen gegenüber anderen Szenariostudien waren dadurch nicht vermeidbar. Annahmen und Vorgehensweise für die Erstellung der Entwicklungspfade sowie Ergebnisse der Modellierung (inklusive vergleichende Einordnung gegenüber anderen Szenariostudien) werden in Kapitel 4 der Langfassung ausführlich begründet und diskutiert.
Im Folgenden werden, nach einem kurzen Überblick über die Randbedingungen für die Pfaderstellung, wichtige Ergebnisse zusammengefasst und Schlussfolgerungen gezogen.
3.1 Auswahl und Begründung der Entwicklungspfade
Den beiden Entwicklungspfaden liegen folgende Grundannahmen zugrunde:
- Jede Grundstoffindustrie erreicht bis 2045 einzeln nahezu Klimaneutralität.
- Die inländischen Produktionsmengen für die Grundstoffe verbleiben auf einem ähnlichen Niveau wie heute.
- Restriktionen in Bezug auf die Ressourcenverfügbarkeit (erneuerbarer Strom, Biomasse, Altkunststoffe etc.) werden berücksichtigt.
- Die Pfade repräsentieren hinsichtlich der wirtschaftlichen, infrastrukturellen, regulatorischen und gesellschaftlichen Rahmenbedingungen plausible und realistische Entwicklungen (keine Extremannahmen).
- Beide Pfade sind konsistent mit Annahmen über die Entwicklung des Gesamtsystems der übrigen Branchen und Sektoren in Deutschland.4
Große Bedeutung kommt der Abschätzung künftiger Energieträgerpreise zu. Diese beeinflussen, da Energieträger und -verbrauch zwischen den verschiedenen Vermeidungstechnologien variieren, die Produktionskosten und damit die relative Bedeutung der Technologien stark. Als Basis für die Abschätzungen dienten Preisprognosen der Internationalen Energieagentur von 2021. Während der gutachterlichen Arbeit an den Entwicklungspfaden brach der russische Angriffskrieg gegen die Ukraine aus, was seriöse Prognosen zu den mittel- und längerfristigen Entwicklungen bei Energieträgerpreisen, Rohstoffverfügbarkeiten oder Produktnachfragen unmöglich machte. Um die veränderte Ausgangslage dennoch in angemessener Weise zu berücksichtigen, wurden in den Entwicklungspfaden auf die Rolle von Erdgas als Brückentechnologie hin zu einer Wasserstoffwirtschaft verzichtet und angenommen, dass bis 2030 keine Zunahme des Erdgasbedarfs in den drei Grundstoffindustrien stattfindet.5 Dafür muss Wasserstoff bereits früher in großen Mengen verfügbar gemacht werden.
Als Unterscheidungsmerkmal für die beiden Entwicklungspfade wurde der internationale Kooperationsgrad gewählt: Während in Pfad A eine weitgehend nationale Strategie verfolgt wird, baut Pfad B auf internationaler Kooperation auf (0). Eine Diskussion der Vor- und Nachteile von internationaler Kooperation bzw. von Autarkiebestrebungen in der Grundstoffindustrie erschien zum Zeitpunkt der Pfaderstellung gerade auch angesichts der geopolitischen Umwälzungen infolge des Ukrainekriegs, durch welche die extremen Abhängigkeiten Deutschlands von ausländischen (Energie-)Ressourcen sehr deutlich wurden, angezeigt.
Szenarien für die Erstellung der Entwicklungspfade |
---|
Entwicklungspfad A: wenig internationale Kooperation In diesem Szenario mit gegenüber heute deutlich geringerer internationaler Kooperation sollen Abhängigkeiten, insbesondere von Importen, minimiert werden; die Rohstoffproduktion findet soweit möglich in Deutschland statt. Dies reizt energetische und materielle Effizienzverbesserungen an, zudem werden Recyclingquoten z. B. für Metalle oder Kunststoffe erhöht. Der Einsatz von CO2-Abscheidung wird wegen möglicher Akzeptanzprobleme für inländische Speicherstätten und schlechter CO2-Exportmöglichkeiten geringgehalten, findet jedoch dann statt, wenn dadurch die Importabhängigkeit bei grünem Wasserstoff entschärft werden kann. Trotzdem notwendige Wasserstoffimporte kommen überwiegend bis komplett aus Europa. Inländische Biomasse wird (wie heute schon) ausgereizt.
Entwicklungspfad B: viel internationale Kooperation In diesem Szenario mit viel internationaler Kooperation (d. h. mindestens dem heutigen Niveau in einer eng vernetzten Weltwirtschaft entsprechend) sind Importe von grünen Energieträgern und Rohstoffen, wie Wasserstoff, Methanol und bedingt auch Biomasse, über gut ausgebaute europaweite Netze möglich und werden forciert. Gute Exportmöglichkeiten für CO2 senken die Hürden für den Einsatz der CO2-Abscheidung. Dies führt umgekehrt dazu, dass Effizienzanstrengungen nicht über das heutige Maß hinaus angestoßen werden. |
3.2 Zentrale Ergebnisse je Grundstoffindustrie
3.2.1 Eisen/Stahl
Bei Eisen/Stahl erfordert ein Technologiewechsel auf das wasserstoffbasierte Direktreduktionsverfahren den Neubau der Produktionsanlagen. Das Zeitfenster hierfür öffnet sich jeweils, wenn ein Hochofen das Ende seiner Nutzungszeit erreicht. Die Entwicklungspfade können daher auf Ebene der einzelnen Standorte bzw. Anlagen beschrieben werden. Der Umstellungsfahrplan orientiert sich an den jeweiligen Zeitpunkten der angenommenen Neuerrichtungen der Hochöfen. Für die Pfaderstellung wurden die (bis zu diesem Zeitpunkt) kommunizierten Transformationsstrategien der Anlagenbetreiber herangezogen.
Entwicklungspfad A (wenig Kooperation)
Durch die überwiegend national ausgerichtete Strategie wird die Entwicklung insbesondere durch die limitierte Verfügbarkeit an inländisch erzeugtem grünem Wasserstoff bestimmt. Daher werden drei große Hochöfen nicht auf das DR-Verfahren umgestellt, stattdessen aber mit CO2-Abscheidung nachgerüstet und zur Erreichung höchstmöglicher Energieeffizienz umfassend modernisiert. Auf die Restriktionen wird zusätzlich mit einem generell effizienteren Materialeinsatz (z. B. im Stahlbau) und mit Materialsubstitution reagiert, was bis 2050 in einem Rückgang der Stahlnachfrage von 10 % (gegenüber der Fortführung des historischen Trends) resultiert. In Verbindung mit einer Steigerung der Kapazitätsauslastung der verbleibenden Stahlwerke führt dies in Pfad A zur Stilllegung von fünf Stahlwerken (mit einer Produktionskapazität von 8,4 Mio. t Stahl/Jahr). Die Zusammensetzung der Produktionstechnologien wandelt sich im Modell erst ab etwa 2030, dann jedoch deutlich: Bis 2050 ersetzen die wasserstoffbasierten Routen Direktreduktion mit Schmelzofen und Konverter (24 %, bezogen auf die produzierte Stahlmenge) und Direktreduktion mit Lichtbogenofen (25 %) die Hochofenroute, welche dann nur noch in Kombination mit CO2-Abscheidung produziert (18 %). Die Produktionsmenge der Stahlschrottroute bleibt nahezu konstant.
Entwicklungspfad B (viel Kooperation)
Die besseren Importmöglichkeiten für grünen Wasserstoff führen zu geringeren Effizienzbemühungen beim generellen Energie- und Materialeinsatz, weshalb die Stahlnachfrage nur moderat zurückgeht. Bis 2036 werden so im Modell nur zwei kleinere Stahlwerke (mit einer Produktionskapazität von 3,7 Mio. t Rohstahl/Jahr) stillgelegt. Die Umstellung auf wasserstoffbasierte Produktionsverfahren wird konsequenter als in Pfad A vorangetrieben, sodass nur ein Hochofen (dann mit CO2-Abscheidung) im Bestand verbleibt. Die Zusammenstellung der verschiedenen Produktionsrouten wandelt sich schon ab etwa 2025 deutlich: Bis 2030 tragen die wasserstoffbasierten Routen (mit Schmelzofen und Konverter: 16 %; mit Lichtbogenofen: 15 %) bereits substanziell zur gesamten Stahlproduktion bei, bevor 2050 nur noch 5 % des Stahls auch dem Hochofen stammen. Der Anteil der Stahlschrottroute bleibt auch hier nahezu konstant.
Einordnung und Vergleich der Entwicklungspfade
In beiden Pfaden sinkt der Endenergiebedarf zwischen 2022 und 2045 deutlich um knapp die Hälfte auf ca. 350 PJ/Jahr. Grund dafür ist vor allem der geringere energetische Bedarf der Eisenerzreduktion bei Verwendung von Wasserstoff anstelle von Kohle.6 Wasserstoff macht etwa ein Drittel (Pfad A; 2045: 114 PJ) bzw. die Hälfte (Pfad B; 2045: 173 PJ) des Endenergieverbrauchs aus. Bezüglich der THG-Emissionen weist Pfad B einen kumulierten Vorteil auf, denn die Umstellung beginnt hier rund fünf Jahre früher als in Pfad A. Bis 2045 reduzieren sich die THG-Emissionen in beiden Pfaden um rd. 90 %. Dies wird allerdings nur dann erreicht, wenn konsequent bei jeder Investitionsentscheidung zur Neuzustellung eines Hochofens auf emissionsarme Technologien umgestellt wird. Schnellere Reduktionen wären technisch machbar, wären aber für die Betreiber mit hohem Aufwand und Risiken verbunden, da mehrere Anlagen zeitgleich umgestellt werden müssten.
Mit Blick auf die Wirtschaftlichkeit ergibt sich ein interessantes Bild. Beide Pfade produzieren 2045 Rohstahl zu nahezu gleichen spezifischen Kosten von rd. 520 Euro/t Rohstahl (Abb. 3.1 links) und damit über 35 % teurer als das Vorkrisenniveau vor der Covid-19-Pandemie und dem Ukrainekrieg (mittlere Produktionskosten 2015–2019: 380 Euro/t Rohstahl).
Abb. 3.1 Produktionskosten Stahl
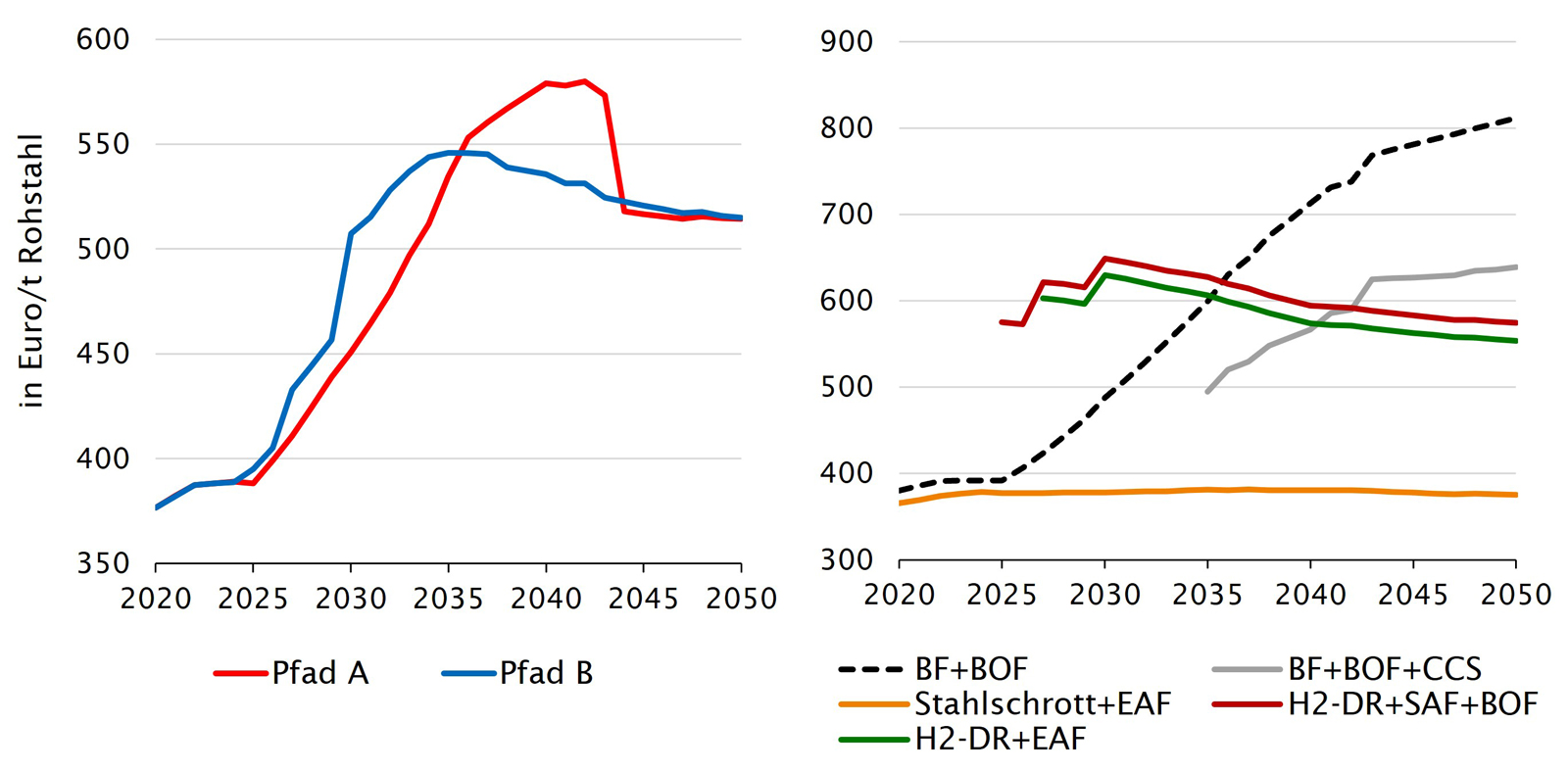
rechts: spezifische Produktionskosten nach Route für Entwicklungspfad B
Hinweis: Berechnungen auf Grundlage von Kostenprognosen vor Beginn des
Ukrainekriegs
Eigene Darstellung nach Prognos/Wuppertal Institut 2022
Jedoch ist der zeitliche Verlauf der Mehrkosten klar verschieden: In Pfad A werden die Kostensteigerungen bei CO2-Emissionszertifikaten später als in Pfad B stabilisiert, während der frühere und stärkere Technologiewechsel von Pfad B zu deutlich höheren Investitions- und Betriebskosten schon ab 2025 führt (Preistreiber ist vor allem der extern bezogene Wasserstoff). Die Abbildung 3.1 rechts zeigt exemplarisch für Pfad B die spezifischen Produktionskosten je Route (ähnliche Werte ergeben sich für Pfad A). Es fällt auf, dass alle drei emissionsarmen Routen in einem ähnlichen Korridor von 500 bis 600 Euro/t Rohstahl liegen, sodass sich hieraus keine Präferenz für eine Technologieoption ableiten lässt. Abgebildet sind ferner die projizierten Produktionskosten der konventionellen Hochofenroute (gestrichelte Linie): Demnach wird die Kostenparität zwischen konventionellen und wasserstoffbasierten Routen Mitte der 2030er Jahre erreicht, danach ist grüner Stahl günstiger.
3.2.2 Zement
Die bestehenden Zementwerke können zu jeder Zeit auf die Vermeidungstechnologien umgestellt werden. Der Umstellungsfahrplan für neue Zemente und Bindemittel richtet sich nach den Genehmigungs- und Zulassungsverfahren. Einige der hier diskutierten Zemente und Bindemittel waren zum Zeitpunkt der Pfaderstellung weder genormt noch zugelassen.
Entwicklungspfad A (wenig Kooperation)
Ziel von Pfad A ist eine weitestgehende Reduktion der CO2-Emissionen durch klinkerarme Zemente, neue Bindemittelsysteme und Materialeffizienz, um den Bedarf an CO2-Abscheidung zu reduzieren. Als Basis für die Projektion der künftigen Produktionsmengen an Zement in Deutschland diente die bisherige Entwicklung. In der national ausgerichteten Strategie von Pfad A wurde zusätzlich der Materialsubstitution und -effizienz eine wichtige Rolle zugeschrieben. Dadurch werden bis 2040 Einsparungen beim Zement von insgesamt bis zu 1,8 Mio. t/Jahr angenommen.
Der Hochlauf der alternativen Routen wird ab 2025 erwartet. Bis 2035 überwiegen die klinkerarmen hüttensandhaltigen Zemente. Danach reduziert sich deren Marktanteil aufgrund der abnehmenden Verfügbarkeit an Hüttensand bis 2050 auf noch 7 %. An ihre Stelle treten ab 2035 klinkerarme Zemente auf der Basis von calcinierten Tonen, die bis 2050 mit einem Anteil von ca. 50 % hohe Bedeutung einnehmen. Die alternativen Bindemittel kommen erst ab 2030 ins Spiel, erreichen aber infolge der beschriebenen Innovationshemmnisse nur geringe Marktanteile von max. 13 %. Die konventionellen Zementarten werden für bestimmte anspruchsvolle Anwendungsgebiete im Tief- und Hochbau voraussichtlich auch nach 2030 alternativlos bleiben. So wurde angenommen, dass sie 2050 noch einen Anteil von 30 % an der Gesamtproduktion aufweisen. Simultan wird ab 2025 die Oxyfuel-CCS-Technologie implementiert, wobei sich der Hochlaufpfad infolge steigender Kosten für CO2-Emissionszertifikate ab 2030 beschleunigt. Um die Minderungsziele zu erreichen, müssen bis 2045 schließlich 75 % der Zementproduktion mit CO2-Abscheidung ausgerüstet werden.
Entwicklungspfad B (viel Kooperation)
Infolge der besseren CO2-Exportmöglichkeiten sinken die Hürden für den Einsatz von Oxyfuel-CCS. Dies reduziert auch den Druck auf Effizienz, sodass bis 2050 eine nahezu konstante Zementproduktion angesetzt wird.
Der Einsatz von klinkerarmen Zementen und neuen Bindemitteln verläuft im Vergleich zu Pfad A weniger forciert. Auch in Pfad B haben die klinkerarmen Zemente mit Hüttensand bis 2035 einen dominierenden Anteil. Da die wasserstoffbasierte Transformation der Stahlindustrie jedoch konsequenter vorangetrieben wird, fällt ab 2030 weniger Hüttensand an als in der Zementindustrie benötigt wird (Abb. 3.2), sodass Hüttensand importiert werden muss.
Abb. 3.2 Entwicklungspfad B: Hüttensandbedarf und -verfügbarkeit
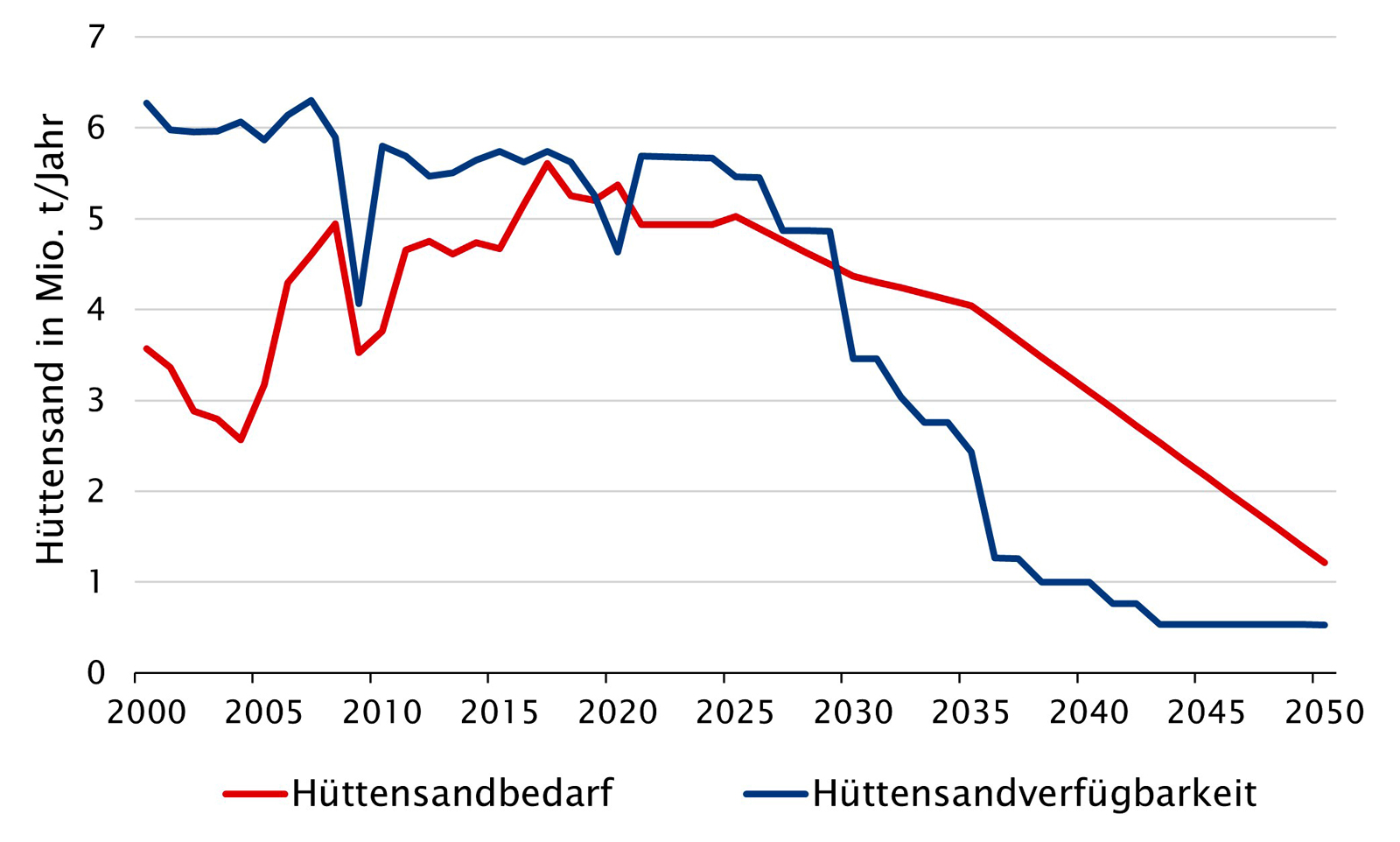
Bis 2050 beläuft sich die Fehlmenge auf rd. 30 Mio. t. Trotz viel internationaler Kooperation ist aber fraglich, ob diese Mengen auf dem Weltmarkt noch verfügbar sein werden, weil auch andere Länder ihre Grundstoffindustrien transformieren. Da für die klinkerarmen Zemente mit calcinierten Tonen in Pfad B eine etwas langsamere Entwicklung als in Pfad A angenommen wird, kommt den klinkerreichen Zementen höheres Gewicht zu. Sie sinken im Modell etwas langsamer als in Pfad A und haben 2050 noch einen Anteil von ca. 35 %. Für die neuen Bindemittelsysteme wird ein maximaler Marktanteil von 10 % angenommen. Unter diesen Annahmen müssen bis 2050 ca. 90 % der Zementproduktion mit CO2-Abscheidung ausgerüstet werden, um die Minderungsziele erreichen zu können.
Einordnung und Vergleich der Entwicklungspfade
Die Entwicklung der beiden Entwicklungspfade läuft ähnlich, aber nicht gleich. 2050 wird in Pfad A ein Klinkerfaktor von 52 % erreicht, in Pfad B von 55 %. Ein stärkerer Unterschied betrifft die Entwicklung der CO2-Abscheidung. Bis 2045 werden in Pfad A 12,5 und in Pfad B 15,5 Mio. t/Jahr CO2 abgeschieden.
Der modellierte Energiebedarf der Zementproduktion divergiert für die beiden Pfade nur geringfügig, sowohl in Bezug auf den Gesamtenergiebedarf als auch auf die eingesetzten Energieträger. Nach einem leichten Rückgang durch den sinkenden Anteil an Zementklinker steigt der Energiebedarf ab 2035 u. a. aufgrund des Strombedarfs für die CO2-Abscheidung wieder an und erreicht 2045 mit 100 PJ/Jahr ein ähnliches Niveau wie heute. Die Entwicklung der THG-Emissionen folgt im Wesentlichen dem Hochlaufpfad der CO2-Abscheidung: In Pfad A werden Netto-null-Emissionen erst 2050 erreicht, in Pfad B bereits 2043 und anschließend – durch die Verwendung biogener Brennstoffe im Verbund mit CCS – sogar negative Emissionen (2050 in Höhe von 1,9 Mio. t CO2-eq/Jahr).
Abb. 3.3 Spezifische Kosten der Zementherstellung
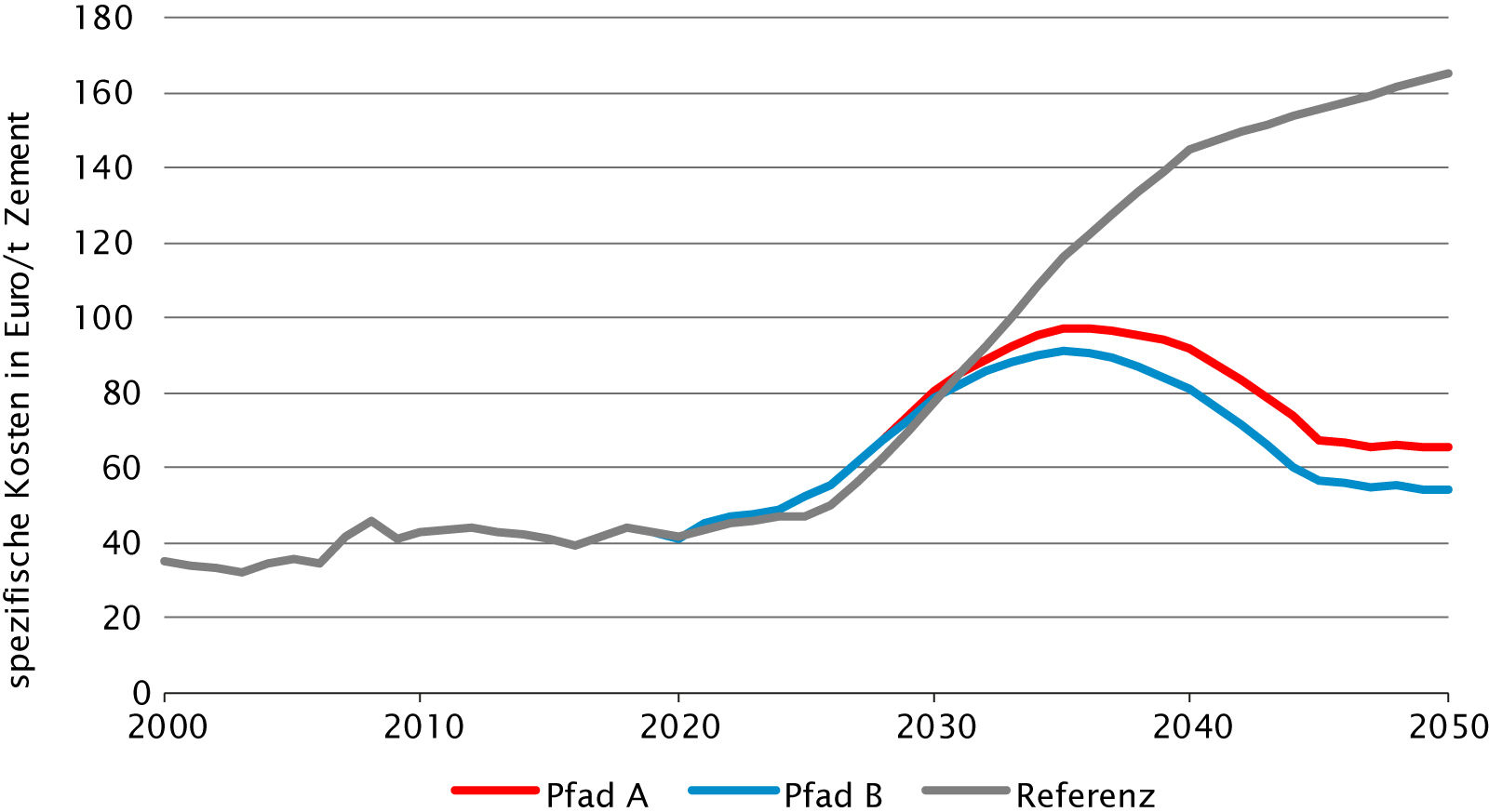
Ukrainekriegs
Eigene Darstellung nach Prognos/Wuppertal Institut 2022
Mit Blick auf die Wirtschaftlichkeit ergibt sich folgendes Bild. Die Produktionskosten liegen 2045 in Pfad A bei 67 Euro/t Zement und damit ca. 60 % über dem Vorkrisenniveau (mittlere Produktionskosten 2015–2019: ca. 42 Euro/t Zement). In Pfad B wird Zement 2045 etwas günstiger produziert (57 Euro/t Zement). Der wichtigste Kostentreiber ist die CO2-Bepreisung, die erst ab 2035 durch den verstärkten Einsatz von CO2-Abscheidung zunehmend kompensiert werden kann. Die Parität mit dem Referenzpfad (Produktion konventioneller Zemente ohne CO2-Abscheidung) wird 2030 erreicht, danach ist die klimafreundliche Zementproduktion günstiger (Abb. 3.3).
3.2.3 HVC
Für beide Pfade wurden die zukünftigen Produktionsmengen an HVC in Deutschland gemäß dem Trend der letzten 10 Jahre bis 2050 fortgeschrieben. Aufgrund der großen Unsicherheiten in Bezug auf die Entwicklung der regionalen und internationalen Verfügbarkeiten von Rohstoffen für die HVC-Produktion (vor allem H2, CO2, Methanol, Altkunststoff und Biomasse) musste zum Teil ein pauschaler externer Bezug unterstellt werden, bei dem die Rohstoffe über einen freien Markt besorgt werden. Damit sind regionale, inländische oder auch internationale Bezugsquellen gemeint, deren Prozesse nicht explizit in den Entwicklungspfaden abgebildet sind und die deshalb nicht (direkt) der HVC-Produktion zugeordnet werden.
Entwicklungspfad A (wenig Kooperation)
Im überwiegend national ausgerichteten Pfad A wird die Umstellung auf den elektrischen Steamcracker forciert, um die CO2-Abscheidung gering zu halten. Nach 2040 tragen konventionelle Cracker, die mit CO2-Abscheidung nachgerüstet wurden, nur noch ca. 8 % zur Gesamtkapazität der Steamcracker bei. Die MtO-/MtA-Route wird wegen der schwach ausgeprägten Importmöglichkeiten für grünes Methanol nicht stark verfolgt. Bis 2050 werden im Modell 15 % der HVC-Produktion über die MtO-/MtA-Route abgedeckt.
Zur Reduktion der rohstoffbedingten THG-Emissionen wird für synthetisches Naphtha ein ambitionierter Hochlaufpfad unterstellt, sodass bis 2050 ein Anteil von 40 % am Rohstoffeinsatz in den Crackern erreicht wird. Um Importe möglichst gering zu halten, wird angenommen, dass die HVC-Produzenten langfristig den überwiegenden Teil (85 %) des benötigten synthetischen Naphthas bzw. grünen Methanols für die MtO-/MtA-Route selber herstellen. Der dafür nötige Wasserstoff wird im Modell zu 35 % mittels Elektrolyse gewonnen, weitere 17 % können aus Nebenprodukten des Steamcrackers bereitgestellt werden; knapp die Hälfe (bis 2045 rd. 1,3 Mio. t Wasserstoff) muss jedoch extern auf dem Markt bezogen werden. Der erforderliche Kohlenstoff wird zu einem Viertel durch Biomassevergasung bereitgestellt, drei Viertel müssen extern bezogen werden. Schließlich werden in Pfad A die deutschen Potenziale für chemisches Recycling von Altkunststoffen zur Herstellung von Pyrolyseöl als Naphthaersatz ausgereizt (bis 2045 ca. 2,9 Mio. t Altplastik/Jahr).
Entwicklungspfad B (viel Kooperation)
Auch in Pfad B spielt die Umstellung auf den elektrischen Steamcracker eine bedeutende Rolle. Wegen der besseren Importmöglichkeiten für grünes Methanol wird die MtO-/MtA-Route aber stärker ausgebaut, sodass bis 2050 ein Drittel der HVC damit hergestellt werden. Ferner verbleiben in Pfad B etwas höhere konventionelle Steamcrackerkapazitäten im Bestand, die mit CO2-Abscheidung nachgerüstet werden (rd. 15 % gemessen an der Gesamtkapazität an Steamcrackern).
Bei den Rohstoffen werden der internationalen Ausrichtung entsprechend grünes Methanol und synthetisches Naphtha zu mehr als zwei Dritteln auf dem (internationalen) Markt eingekauft. Der Rest wird durch Eigenproduktion bereitgestellt. Der dafür nötige Wasserstoff wird zu zwei Dritteln extern bezogen (bis 2045 rd. 0,8 Mio. t/Jahr H2), weitere 25 % fallen als Nebenprodukt der Steamcracker an, sodass lediglich 8 % mittels Elektrolyse selber hergestellt werden müssen. Beim Kohlenstoff werden drei Viertel der benötigten Menge auf dem Markt eingekauft, der Rest durch Biomassevergasung produziert.
Einordnung und Vergleich der Entwicklungspfade
Beide Entwicklungspfade zeichnen sich durch einen Wechsel von fossilen Brennstoffen als Hauptenergieträger hin zu Strom aus. Infolge des unterschiedlichen Rohstoffbezugs divergiert der Gesamtstrombedarf jedoch stark: In Pfad A ergibt sich durch den Fokus auf Eigenproduktion bis 2045 mehr als eine Verdopplung des Strombedarfs (339 PJ/Jahr) gegenüber Pfad B (157 PJ/Jahr).7 Dafür verantwortlich ist vor allem die Eigenproduktion von Wasserstoff durch Elektrolyse, die bis 2045 in Pfad A einen rund 10-mal höheren Bedarf an erneuerbarem Strom (163 PJ/Jahr) auslöst als in Pfad B.
Die prozessbedingten THG-Emissionen entwickeln sich in beiden Pfaden ähnlich und gehen von heute 8 Mio. t CO2-eq/Jahr bis 2042 auf Netto-null zurück. Durch den kombinierten Einsatz von Biomasse und CO2-Abscheidung sind danach leichte negative Gesamtemissionen möglich. Die rohstoffbedingten THG-Emissionen (von aktuell 11 Mio. t CO2-eq/Jahr für die Herstellung von fossilem Naphtha) sind durch die in den Pfaden unterstellte Umstellung auf grüne Rohstoffe vollständig vermeidbar.
Gegenüber dem Vorkrisenkostenniveau (mittlere Produktionskosten 2015–2019: ca. 790 Euro/t HVC) verteuert sich die HVC-Produktion in den Entwicklungspfaden bis 2045 um ca. 130 % (Pfad A) bzw. 90 % (Pfad B) markant. Im Vergleich zum Referenzpfad (Produktion der entsprechenden HVC-Mengen über fossiles Naphtha in konventionellen Steamcrackern, mit CO2-Kosten gemäß EU-ETS-Preispfad) verteuern sich die Produktionskosten bis 2045 um etwa 50 % (Pfad A) bzw. 26 % (Pfad B) (Abb. 3.4). Im Gegensatz zu Stahl und Zement liegen die Produktionskosten der klimafreundlichen Verfahren damit für den gesamten Betrachtungszeitraum über jenen der konventionellen Herstellungsverfahren. Wesentliche Preistreiber sind die Kosten für die grünen Rohstoffe, vor allem für Wasserstoff.
Abb. 3.4 Spezifische Kosten HVC-Produktion
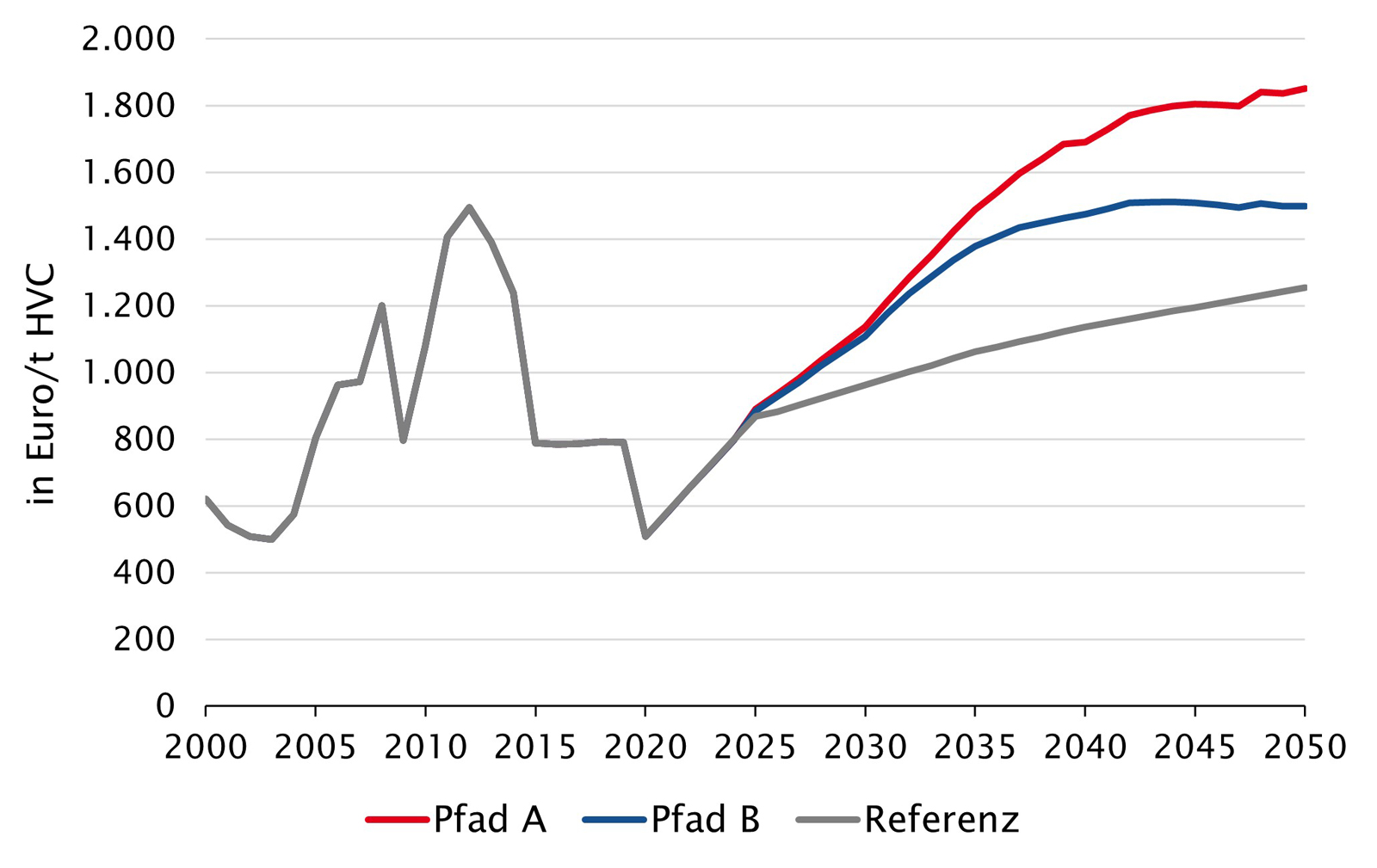
Ukrainekriegs
Eigene Darstellung nach Prognos/Wuppertal Institut 2022
3.3 Gesamtbetrachtung
Der errechnete Gesamtenergiebedarf der drei betrachteten Grundstoffindustrien liegt 2045 in Pfad A bei ca. 780 PJ/Jahr und damit nur minimal unter dem Bedarf von 2020 (785 PJ). Der Gesamtenergiebedarf 2045 in Pfad B liegt rd. 20 % tiefer (rd. 630 PJ/Jahr), was vor allem auf die höhere Energieeffizienz (bezogen auf den Endenergiebedarf) der wasserstoffbasierten Stahlproduktion zurückgeht. Wasserstoff stellt in beiden Pfaden einen zentralen Bestandteil der Produktionsprozesse dar. In Pfad B wird für die Stahlproduktion mehr Wasserstoff verwendet (wegen der stärkeren Umstellung auf Direktreduktion), in Pfad A für die HVC-Produktion (wegen der schlechteren Importmöglichkeiten für synthetisches Naphtha bzw. grünes Methanol). Insgesamt werden bis 2045 in Pfad A 3,6 Mio. t/Jahr Wasserstoff eingesetzt und damit rund ein Drittel mehr als in Pfad B (insgesamt 2,6 Mio. t/Jahr). Beim Strombedarf sind für 2045 449 PJ/
Jahr (Pfad A) bzw. 276 PJ/Jahr (Pfad B) zu veranschlagen, was gegenüber 2020 eine Steigerung um das 5- (Pfad A) bzw. 3-Fache (Pfad B) bedeutet. Der hohe Strombedarf in Pfad A geht vor allem auf die Eigenerzeugung eines beträchtlichen Teils des Wasserstoffs für die HVC-Produktion zurück, was hier einer stärkeren Reduktion der Importabhängigkeiten dient.
Hinsichtlich der Produktionskosten ist Pfad A von stärkeren Preisanstiegen geprägt als Pfad B. Gründe sind die höhere Eigenproduktionsquote, der höhere Energiebedarf und langsamer sinkende CO2-Emissionen im Szenario mit hohem Selbstversorgungsgrad. Gegenüber einer auf internationale Kooperation ausgerichteten Strategie stellt Pfad A auch höhere Anforderungen an die Verfügbarkeit von erneuerbaren Energien und inländisch erzeugtem Wasserstoff. Im Umkehrschluss bedeutet dies, dass ohne einen massiven Ausbau der erneuerbaren Energien, der Wasserstoffproduktion und der benötigten Infrastrukturen die hohen Abhängigkeiten bei Energieträgern und Rohstoffen vom Ausland bestehen bleiben bzw. weiter verstärk werden.
3.4 Ökonomische Effekte
Das für die Modellierung der Entwicklungspfade erstellte Datengerüst erlaubte es, die Effekte der Transformation für eine Reihe von ökonomischen Kennzahlen quantitativ abzuschätzen. Der Umstieg auf emissionsarme Technologien impliziert den Aufbau neuer bzw. den Umbau bestehender Produktionsanlagen. Die kumulierten, über beide Entwicklungspfade gemittelten 8 Mehrinvestitionen (gegenüber einer Referenzentwicklung ohne Klimaschutz) belaufen sich in der HVC-Produktion auf 2,2 Mrd. Euro, in der Zementherstellung auf 4,1 Mrd. Euro und in der Stahlproduktion auf 8,6 Mrd. Euro (in der Summe 14,9 Mrd. Euro). Davon gehen Wachstumsimpulse auf die Gesamtwirtschaft aus, welche sich aufgrund positiver Rückkopplungen weiter verstärken. So führen die erforderlichen Anlagenumstellungen zu Mehrinvestitionen auch in anderen Wirtschaftsbereichen (vor allem im Anlagenbau). Gemäß der Modellierung erhöhen sich dadurch die Gesamtinvestitionen bis 2050 auf 22 Mrd. Euro. Durch die Investitionen steigt das Lohneinkommen der privaten Haushalte, was wiederum den privaten Konsum um knapp 6 Mrd. Euro anheben könnte. Ein Teil der Mehrnachfrage nach Investitions- und Konsumgütern wird importiert (laut Modellierung gesamthaft 11 Mrd. Euro). Die Klimainvestitionen in den drei betrachteten Grundstoffindustrien führen so insgesamt zu einer kumulativen Erhöhung des Bruttoinlandprodukts von ca. 16 Mrd. Euro.
Außerdem wurde untersucht, wie sich die transformationsbedingten (temporär) höheren Produktionskosten bei Stahl, Zement und HVC auf die Preise von Endprodukten, die aus diesen Grundstoffen hergestellt werden, auswirken. Unter der vereinfachenden Annahme, dass in den nachgelagerten Produktionsbereichen die Kostensteigerungen beim Bezug der Grundstoffe vollständig weitergegeben werden, erhöhen sich die Preise der Endprodukte in Abhängigkeit von der relativen Bedeutung der Vorleistungen der jeweiligen Grundstoffindustrie:
Eine klimafreundliche Stahlherstellung ist gemäß der Modellierung Ende der 2020er Jahre maximal 42 % teurer als die konventionelle. Mitte der 2030er Jahre wird die Kostenparität erreicht und bis 2045 ist grüner Stahl 28 % günstiger als konventionell hergestellter. Davon am stärksten betroffen sind erwartungsgemäß die Herstellung von Metallerzeugnissen sowie der Maschinen- und der Fahrzeugbau. So würde sich z. B. ein Personenkraftwagen im Wert von 30.000 Euro um maximal 480 Euro verteuern, 2045 wäre derselbe Wagen um 330 Euro günstiger.
In der Zementherstellung liegen die Produktionskosten emissionsarmer Verfahren (Einsatz von Oxyfuel-CCS) lediglich bis Ende der 2020er Jahre maximal 10 % über denjenigen der konventionellen. Eine Bauproduktion im Wert von 100.000 Euro würde sich dadurch schätzungsweise um 100 Euro verteuern. Bis 2045 sind grüne Zemente gemäß der Modellierung um ca. 60 % günstiger; dieselbe Bauproduktion wäre somit ca. 640 Euro günstiger.
Eine klimafreundliche HVC-Produktion bleibt hingegen dauerhaft teurer als die konventionelle (max. Kostensteigerung von 53 % Ende der 2030er Jahre in Pfad A). Ein Medikament, das vor dem Umstieg auf emissionsarme Produktionsverfahren 100 Euro kostet, würde sich so um maximal 5,64 Euro verteuern.
Zusammenfassend scheinen die nachgelagerten Produktionsbereiche hinsichtlich ihrer preislichen Wettbewerbsfähigkeit somit nur in einem geringen Umfang von der Transformation der drei untersuchten Grundstoffindustrien betroffen zu sein. Zu beachten ist allerdings, dass solche Modellierungen nicht frei von Unsicherheiten sind. Außerdem basieren die Analysen auf den vor Beginn des Ukrainekriegs abgeschätzten Preisentwicklungen.
4 Auswirkungen, Chancen und Risiken der Transformation
Weitere Auswirkungen der Transformation wurden im TA-Projekt mithilfe von qualitativen Analysen und Plausibilitätsüberlegungen behandelt, da eine modelltechnische Abbildung der Effekte mit den eingesetzten Werkzeugen nicht möglich war. Dies betrifft ökologische und Nachhaltigkeitsaspekte der Transformation, mögliche Auswirkungen auf Arbeitsplätze, Wertschöpfungsketten und Importabhängigkeiten sowie Risiken für die Wettbewerbsfähigkeit der deutschen Grundstoffindustrie.
4.1 Ökologische und weitere Nachhaltigkeitsaspekte
Im TA-Projekt wurden ausgewählte ökologische und weitere die Nachhaltigkeit betreffende Effekte durch die Umstellungen in den Produktionsverfahren diskutiert. Ökologische Effekte der Energiebereitstellung, die künftig vor allem durch erneuerbare Energien erfolgen soll und somit Aspekte wie Flächenbeanspruchung, indirekte THG-Emissionen oder die Freisetzung giftiger Luftschadstoffe umfasst, wurden hingegen nicht weiter vertieft.
Auch die klimafreundlichen Produktionsprozesse verursachen mitunter noch CO2-Emissionen. Wenngleich diese nur einen Bruchteil der konventionellen Produktionsprozesse ausmachen, so können Anstrengungen zur Reduzierung der Restemissionen unternommen werden. Ein Beispiel ist Stahlproduktion mit wasserstoffreduziertem Roheisen, wo aus verfahrenstechnischen Gründen sowie zur Einstellung des Kohlenstoffgehalts im Stahl Kohlenstoff wieder zugeführt werden muss, was mit CO2-Emissionen verbunden ist. Derzeit wird in Forschungsprojekten untersucht, ob der zu diesem Zweck bisher verwendete fossile Kohlenstoff durch biogene Rohstoffe substituiert werden kann.
Die Reduktion des Klinkeranteils in klinkerarmen Zementen führt generell dazu, dass die Zusammensetzung der Zemente immer komplexer wird, die Anforderungen an die Komponenten steigen und der Bedarf an chemischen Zusatzmitteln erhöht wird. Wie dies die Nachhaltigkeit der Zemente und die Recyclingfähigkeit von Altbeton beeinflusst, ist derzeit noch ungeklärt. Die Notwendigkeit für alternative Zumahlstoffe wie Tonminerale setzt die Erschließung neuer Lagerstätten voraus, was mit den entsprechenden Umweltauswirkungen verbunden ist. Weil lagerstättenabhängige mineralogische Eigenschaften bedeutende Auswirkungen auf die Eignung der Tone als Zumahlstoffe zu haben scheinen, könnte es künftig möglicherweise ein deutlich breites Portfolio an regionalen Zementen mit kleinteiligen Anwendungsfeldern geben, als bisher angenommen wird.
Bei den diskutierten Technologien des chemischen Recyclings zur Erzeugung von Pyrolyseöl als Naphthaersatz für die HVC-Produktion sind in Bezug auf die Umweltauswirkungen noch viele Fragen offen. Zwar existieren erste ökobilanzielle Bewertungen, diese lassen jedoch in Bezug auf Methodik, Datenlage und Rahmenbedingungen nur eingeschränkte Interpretationen der Ergebnisse zu. Auch das Umweltbundesamt weist darauf hin, dass die Verfahren des chemischen Recyclings sich mit den etablierten Verfahrenswegen (werkstoffliches Recycling, energetische Verwertung) messen lassen müssen und der Nachweis ihrer ökologischen und wirtschaftlichen Vorteilhaftigkeit noch erbracht werden muss.
4.2 Arbeitsplatzeffekte
Für die Stahlindustrie wurde in den Entwicklungspfaden eine leichte Abnahme der Produktionsmenge bis 2045 unterstellt, woraus sich bei gleicher Arbeitsproduktivität ein moderater Rückgang der Beschäftigtenzahl ableitet. Durch die Transformation verändern sich aber auch die Arbeitsprozesse im Stahlwerk. Fachleute schätzen den Personalbedarf der neuen wasserstoffbasierten DR-Anlagen u. a. wegen der höheren Automatisierung als geringer ein im Vergleich zum heutigen Hochofen (bezogen auf identische Produktionskapazitäten der Anlagen). Außerdem entfallen Arbeitsplätze für die Kohleaufbereitung u. a. in den Kokereien. Diesen Beschäftigungsverlusten stehen aber neue Arbeitsplätze in einer künftigen Wasserstoffwirtschaft gegenüber, sodass Expert/innen insgesamt einen positiven Beschäftigungseffekt der Transformation erwarten.
In der Zementindustrie ist die Arbeitsproduktivität in den letzten 15 Jahren leicht angestiegen, weitere Produktivitätsfortschritte (vor allem durch Automatisierung) werden erwartet. Dies und ein (vor allem in Pfad A unterstellter) leichter Rückgang der Produktionsmenge bis 2045 lässt auf künftige Beschäftigungsverluste schließen. Demgegenüber stehen Transformationseffekte, durch welche die Beschäftigungsintensität tendenziell erhöht wird, u. a. komplexere Herstellungsprozesse für klimafreundliche Zemente und Bindemittel, höhere Aufwände für die Bereitstellung hochwertiger Klinkerersatzstoffe oder der zusätzliche Verfahrensschritt der CO2-Abscheidung. Welche dieser gegensätzlichen Wirkungen überwiegen, ist gemäß Expert/innen derzeit noch unklar.
In der HVC-Produktion sind den Beschäftigungsverlusten infolge des (in den Pfaden unterstellten) Produktionsrückgangs die Beschäftigungseffekte durch den veränderten Rohstoffbezug gegenüberzustellen. Im Falle einer verstärkten inländischen Erzeugung der Rohstoffe (wie in Pfad A angenommen) dürften über die gesamte Wertschöpfungskette in Deutschland hinweg mehr Arbeitsplätze geschaffen werden im Vergleich zum gegenwärtig dominierenden Import von Erdöl und dessen Verarbeitung zu Naphtha in Raffinerien.
Der Technologiewechsel führt in den drei betrachteten Grundstoffindustrien auch zu Veränderungen in den benötigten beruflichen Qualifikationen der Beschäftigten. Für die Stahlindustrie erwarten Fachleute zwar keine grundsätzlich neuen Berufsbilder, aber es besteht ein Bedarf an Zusatzqualifikationen, u. a. in Bezug auf den Einsatz von Wasserstoff. Auch für die Zementindustrie werden keine stark veränderten Anforderungen vermutet, jedoch erhöht sich der Komplexitätsgrad der Zementherstellung, zudem steigen die Sicherheitsanforderungen etwa beim Einsatz von Oxyfuel-CCS. In der HVC-Produktion sind neue Anforderungen am ehesten infolge der Umstellung auf die MtO-/MtA-Route zu erwarten, da diese Verfahren bisher in Deutschland nicht angewendet wurden. Schließlich führen die zunehmende Digitalisierung und Automatisierung der Prozesse in allen drei Grundstoffindustrien zu steigenden Qualifikationsanforderungen an das Personal. Ein besseres Verständnis der weiterhin benötigten und infolge der Transformation zusätzlich erforderlichen Qualifikationen ist notwendig, um entsprechende Anpassungen in der beruflichen Aus- und Fortbildung sowie der akademischen Bildung zeitnah vornehmen zu können.
4.3 Auswirkungen auf Wertschöpfungsketten
Die Transformation hat vielfältige Auswirkungen auf die Wertschöpfungsketten innerhalb und zwischen den der drei betrachteten Grundstoffindustrien, aber auch darüber hinaus in vor- und nachgelagerte Branchen. Im Rahmen des TA-Projekts wurde eine Reihe von Wechselwirkungen identifiziert, eine tiefergehende Analyse war allerdings für den vorliegenden Bericht nicht möglich.
Zwischen der Stahl- und der Zementindustrie besteht eine wichtige Wechselwirkung in Bezug auf Hüttensand, der als Nebenprodukt der Hochofenroute anfällt, als Klinkerersatzstoff aber einen wichtigen Rohstoff für die Zementherstellung darstellt, durch den derzeit über 5 Mio. t/Jahr an CO2-Emissionen einspart werden können. Durch die Umstellung der Stahlherstellung auf das Direktreduktionsverfahren nimmt die Verfügbarkeit von Hüttensand sukzessive ab. Falls die klimafreundlichen Stahlherstellungsverfahren keinen adäquaten Ersatz bieten, muss die Zementindustrie künftig andere Klinkerersatzstoffe etablieren, was jedoch mit Herausforderungen verbunden ist.
Zwischen der Zement- und der HVC-Produktion entstehen neue Nutzungskonkurrenzen um Biomasse und Altkunststoffe, die in Zementwerken künftig verstärkt als alternative Brennstoffe und in der HVC-Produktion zur Erzeugung von Rohstoffen eingesetzt werden sollen. Dies hat Auswirkungen auf die Abfallwirtschaft und die kunststoffverarbeitende Industrie, wo Anstrengungen zur Intensivierung der Bioabfallverwertung und des Kunststoffrecyclings nötig sind.
Neue bzw. veränderte Stoffströme ermöglichen Synergien zwischen den drei Grundstoffindustrien. Das künftig in der Stahl- und Zementindustrie aus der Abscheidung anfallende CO2 könnte als Kohlenstoffträger für die HVC-Produktion eingesetzt werden. Der bei der Wasserstoffherstellung mittels Elektrolyse als Nebenprodukt anfallende Sauerstoff kann für die Oxyfuel-CCS-Technologie in der Zementindustrie Verwendung finden.
Aufgrund der Notwendigkeit für die CO2-Abscheidung in der Zementproduktion dürfte die Anbindungsmöglichkeit an eine CO2-Infrastruktur ein wichtiger Standortfaktor bei Entscheidungen über den Weiterbetrieb eines Ofens sein. Dies könnte zu einer gewissen räumlichen Konzentration der Klinkerherstellung führen, was einen erhöhten Bedarf an Klinkertransporten nach sich ziehen könnte mit entsprechenden Rückwirkungen auf den Verkehrssektor.
Durch die Elektrifizierung von Teilen der Produktionsprozesse bei Stahl und HVC (Umstellung auf Lichtbogen-, Schmelzofen oder elektrisch beheizten Steamcrackern, Wasserstoffbereitstellung mittels Elektrolyse) entstehen neue große Stromverbraucher und damit Wechselwirkungen mit dem Stromsystem. Sofern die klimafreundlichen Technologien einen flexiblen Betrieb technisch erlauben (dies trifft voraussichtlich auf den Lichtbogenofen und auf Elektrolyseure mit Protonenaustauschmembran zu), könnten sie mit entsprechenden wirtschaftlichen Anreizen die Einbindung hoher Anteile fluktuierender erneuerbarer Energien in das Stromsystem unterstützen.
Der Maschinen- und Anlagenbau könnte von der Transformation der Grundstoffindustrien deutlich profitieren, da ein hoher Erneuerungs- bzw. Neubaubedarf bei Anlagen und Infrastrukturen in den kommenden zwei Jahrzehnten resultiert, um das Ziel der Klimaneutralität bis 2045 zu erreichen. Aufgrund der Stärke des deutschen Maschinen- und Anlagenbaus kann davon ausgegangen werden, dass ein großer Teil der durch die Transformation angestoßenen zusätzlichen Wertschöpfung in Deutschland stattfinden kann. Dafür müssen aber die Kapazitäten im deutschen Anlagenbau ausgebaut werden.
4.4 Auswirkungen auf die Importabhängigkeiten
Der Energiebedarf der Primärstahlerzeugung wird derzeit hauptsächlich durch importierte Koks- und Steinkohle gedeckt. Der wichtigste Rohstoff ist Eisenerz, das nahezu vollständig importiert wird. Auch nach erfolgter Transformation wird Deutschland auf importiertes Eisenerz angewiesen sein. Im Falle der Route Direktreduktion mit Lichtbogenofen, die höhere, aber derzeit nur begrenzt verfügbare Erzqualitäten erfordert, werden die Importabhängigkeiten tendenziell sogar noch verstärkt. Beim Energiebedarf können die Importabhängigkeiten hingegen reduziert werden, dies allerdings in Abhängigkeit vom Anteil an inländisch erzeugtem Wasserstoff für die Direktreduktion. Durch den verstärkten Einsatz von Lichtbogen- bzw. Schmelzöfen steigt außerdem die Bedeutung von Strom im Energiemix an, der auch künftig inländisch (bzw. Europa) hergestellt werden wird.
In der Zementherstellung ist die Importabhängigkeit bei Brennstoffen und Rohstoffen gegenwärtig sehr gering. Dies wird voraussichtlich auch so bleiben, da beispielsweise Kalkstein als wichtigster Rohstoff meist in unmittelbarer Nähe der Zementwerke gewonnen wird. Beim wichtigen Rohstoff Hüttensand könnte allerdings bei einer gemäß Pfad B voranschreitenden Transformation (mit nur einem verbleibenden Hochofen) die Verfügbarkeit so weit sinken, dass – sofern nicht alternative Hüttensande eingesetzt werden können – die Fehlmenge durch Importe gedeckt werden müsste. Je nach den Transformationspfaden in anderen Staaten dürfte Hüttensand weltweit ein knappes Gut werden.
Die Importabhängigkeit der deutschen HVC-Produktion ist gegenwärtig hoch, da die verwendeten Rohstoffe nahezu vollständig auf Rohöl beruhen. Gemäß den in den Entwicklungspfaden getroffenen Annahmen sollen künftig aber immer größere Anteile der Rohstoffe inländisch hergestellt werden, unter Einsatz von Biomasse, abgeschiedenem CO2, Wasserstoff oder Altkunststoff. Weil diese Ressourcen aber begrenzt sind, bleibt Deutschland voraussichtlich auch in Zukunft zu einem nicht unerheblichen Anteil auf Rohstoffimporte von grünem Naphtha und grünem Methanol für die HVC-Produktion angewiesen.
4.5 Risiken für die Wettbewerbsfähigkeit
In den Entwicklungspfaden wurde unterstellt, dass die inländischen Produktionsmengen der drei betrachteten Grundstoffindustrien bis 2045 gegenüber heute auf einem ähnlichen Niveau verbleiben bzw. aufgrund verbesserter Materialeffizienz beim Einsatz der Grundstoffe nur moderat sinken. Die tatsächliche Entwicklung ist aber ungewiss und davon abhängig, wie gut sich deutsche Unternehmen im internationalen Wettbewerb behaupten können. Im TA-Projekt wurden daher mögliche Gefahren für die Wettbewerbsfähigkeit des Industriestandorts Deutschland diskutiert. Besteht das Ziel die heimische Grundstoffproduktion weitgehend zu erhalten, sind diese Gefahren zu berücksichtigen und Maßnahmen zu ergreifen, um sie so weit wie möglich zu vermeiden.
Weniger Klimaschutz im Ausland (Carbon Leakage)
Vor allem bei Eisen/Stahl und HVC stehen die deutschen und europäischen Hersteller in einem starken internationalen Wettbewerb. Höhere Produktionskosten infolge steigender CO2-Preise im europäischen Emissionshandel oder aufgrund der Umstellung auf emissionsarme Produktionsprozesse führen zu Wettbewerbsnachteilen gegenüber Unternehmen in Weltregionen, die aufgrund von weniger ambitionierten Klimaschutzpolitiken geringere bzw. keine klimaschutzbezogenen Kosten zu tragen haben. Im Ergebnis sind in Europa hergestellte Grundstoffe auf den internationalen Märkten nicht mehr konkurrenzfähig. Es besteht die Gefahr, dass Teile der europäischen Grundstoffproduktion in Länder verlagert werden, in denen weiterhin kostengünstig mit konventionellen Verfahren produziert werden kann (Carbon Leakage). Dies ist aus klima- und industriepolitischer Sicht unerwünscht, denn mit der Verlagerung industrieller Aktivität werden THG-Emissionen lediglich örtlich verlagert, während es in Deutschland zu Beschäftigungsverlusten kommt.
Derzeit liegt der aktuelle CO2-Preis im europäischen Emissionshandel deutlich höher als in anderen großen Wirtschaftsnationen außerhalb der EU. Einige wichtige Schwellenländer (z. B. Indien, Brasilien) nehmen gar keine CO2-Bepreisung vor. Dies und der Umstand, dass Deutschland und die EU deutlich schneller Klimaneutralität erreichen möchten als andere Wirtschaftsnationen, legt nahe, dass Carbon Leakage zukünftig tatsächlich zu einer relevanten Gefahr für den Wirtschaftsstandort Deutschland bzw. Europa werden könnte.
Der Sorge vor Emissionsverlagerungen wird bislang dadurch begegnet, dass Sektoren, die im internationalen Wettbewerb stehen, die Emissionszertifikate kostenlos zugeteilt erhalten. Allerdings mindert dies den Anreiz für Klimaschutzinvestitionen. Die kostenlose Zuteilung soll daher ab 2026 für ausgewählte Industrien (darunter die Eisen/Stahl- und Zementproduktion, nicht aber die HVC-Produktion) schrittweise reduziert und bis 2034 ganz durch ein CO2-Grenzausgleichssystem (Carbon Border Adjustment Mechanism – CBAM) ersetzt werden. Durch den CBAM wird auf entsprechende Importgüter eine Abgabe fällig, die sich an den aktuellen CO2-Preis im europäischen Emissionshandel orientiert.
Mit der Einführung des CBAM (und dem zeitgleichen Auslaufen der kostenlosen Zuteilung von Emissionszertifikaten) sind aber auch Risiken verbunden. Sollte das neue Instrument nicht wie erwartet funktionieren, könnte es verstärkt zu Carbon-Leakage-Effekten kommen. Kritisiert wird außerdem, dass der CBAM in seiner aktuellen Ausgestaltung nicht die Exporte europäischer Unternehmen umfasst, wodurch die teureren europäischen Grundstoffe auf den Märkten anderer Weltregionen ggf. nicht mehr konkurrenzfähig sind. Schließlich besteht das Risiko, dass ausländische Hersteller diejenigen Teile ihrer Grundstoffproduktion, die relativ klimafreundlich sind, in die EU exportieren, dafür aber die heimisch genutzten Grundstoffe CO2-intensiver werden.
Bessere Bedingungen für erneuerbare Energien im Ausland (Green Leakage)
Eine zukünftig klimaneutrale Grundstoffproduktion wird große Mengen an erneuerbaren Energien und grünen Rohstoffen benötigen. Die Potenziale für erneuerbare Energien sind aber in einigen Ländern bzw. Weltregionen erheblich größer als in Deutschland, sodass dort grüne Energieträger und Rohstoffe deutlich günstiger erzeugt werden können. Diese Länder bzw. Regionen werden für die Grundstoffproduktion künftig an Attraktivität gewinnen, wodurch es zu Produktionsverlagerungen und zu einem Rückgang der Produktion in Deutschland kommen könnte (Green Leakage).
Risiken für Green Leakage bestehen aktuell vor allem für die deutsche Stahl- und langfristig auch für die HVC-Produktion. So könnte die wasserstoffbasierte Rohstahlproduktion zukünftig verstärkt in Ländern wie Schweden, Südafrika oder Australien stattfinden, die über gute Bedingungen für erneuerbare Energien und zugleich über hohe Erzvorkommen verfügen. Auch könnten Entwicklungsländer, die als potenzielle Lieferländer für grünen Wasserstoff infrage kommen, künftig bemüht sein, nicht nur Wasserstoff, sondern gleich den damit hergestellten Eisenschwamm (bzw. sogar grünen Stahl) nach Deutschland zu exportieren, um selber stärker an der Wertschöpfung der Stahlproduktion zu partizipieren. Die Erzeugung von grünen Rohstoffen im Ausland für die HVC-Produktion könnte ebenfalls dazu führen, dass HVC in Zukunft aufgrund von Verbundvorteilen verstärkt an diesen Standorten produziert wird.
Während somit bei einer reinen Fokussierung auf die Energie- und Rohstoffkosten eine zukünftige Verlagerung industrieller Produktion durch Green Leakage für Deutschland naheliegend erscheint, müssen auch weitere Standortfaktoren bedacht werden. In Bezug auf diese weisen in vielen Fällen Länder mit besonders günstigen Bedingungen für erneuerbare Energien (z. B. Länder der Region Mittlerer Osten und Nordafrika) auch Risikofaktoren auf. So fehlen dort beispielsweise häufig ausgeprägte industrielle Strukturen, verlässliche politische, rechtliche und sozioökonomische Rahmenbedingungen, eine stabile Energieversorgung oder qualifizierte Arbeitskräfte. Aufgrund der Vielzahl relevanter Standortfaktoren ist es aus heutiger Sicht schwierig vorherzusehen, wie stark Green Leakage die deutsche Grundstoffindustrie in den kommenden Jahren und Jahrzehnten betreffen wird.
Unklare zukünftige Rahmenbedingungen
Neben Carbon und Green Leakage stellen Unsicherheiten über wichtige zukünftige Rahmenbedingungen für die Grundstoffproduktion in Deutschland auch bereits kurzfristig ein Risiko für die Attraktivität des Standorts Deutschland dar. Planungssicherheit ist im anstehenden Transformationsprozess aufgrund der langfristigen Investitionsentscheidungen (mit Lebensdauern der Anlagen von häufig mehreren Jahrzehnten) von besonders hoher Bedeutung. Ausreichende Klarheit über die Produktionsbedingungen in den nächsten Dekaden ist bereits in den kommenden Jahren bis 2030 nötig, in denen in großen Teilen der Grundstoffindustrie bedeutende und langfristige Reinvestitionsentscheidungen anstehen. Dies betrifft nicht nur die regulatorischen (z. B. THG-Reduktionsziele, rechtliche Lage zum Einsatz von CCS), sondern auch die wirtschaftlichen Rahmenbedingungen (z. B. Preise für Energieträger, Rohstoffe oder CO2-Zertifikate, Etablierung grüner Märkte). Bleibt diese Klarheit aus, so erscheint es plausibel, dass Investitionen der entsprechenden Branchen verstärkt in solchen Ländern stattfinden werden, in denen entweder weniger ambitionierte Klimaschutzziele für die nächsten Jahre bzw. Jahrzehnte formuliert wurden oder aber in denen von einer dauerhaft günstigen und ausreichenden Verfügbarkeit für erneuerbare Energieträger und grüne Rohstoffe ausgegangen werden kann.
Hohe Strompreise
Ein großes Hemmnis für Investitionen in klimafreundliche Produktionsprozesse stellen hierzulande auch die derzeit bestehenden Unsicherheiten über die künftigen Preise für (grünen) Strom dar. Da die Elektrifizierung vor allem für die Eisen/Stahl- und Chemieindustrie eine wichtige Option auf dem Weg zur klimaneutralen Grundstoffproduktion darstellt, sind wettbewerbsfähige Strompreise von hoher Bedeutung. Die teilweise extremen Kostensteigerungen bei Strom- und Gaspreisen infolge des Ukrainekriegs haben deutlich gemacht, wie empfindlich industrielle Prozesse generell gegenüber Energiepreisschwankungen sein können. Zwar sind infolge des Kriegsbeginns die Energiepreise auch in anderen Teilen der Welt angestiegen, allerdings nicht so stark wie in Europa, das bisher in hohen Mengen Erdgas aus Russland importierte.
Wettbewerbsnachteile infolge hoher Strompreise zu mindern, gestaltet sich schwierig. Prinzipiell stehen dazu zwei Ansätze (bzw. auch eine Kombination davon) zur Verfügung: Zum einen kann versucht werden, den Strombedarf zu reduzieren, zum anderen können Maßnahmen zur Senkung der Strompreise ergriffen werden. Der erste Ansatz ist aus heutiger Sicht kaum umsetzbar, da die Elektrifizierung und Umstellung auf grüne Rohstoffe, die zu wesentlichen Teilen aus erneuerbarem Strom gewonnen werden sollen, wichtige Elemente der Transformation der Grundstoffindustrien darstellen. Zur Senkung des Strompreises verbleibt – abgesehen von einer staatlichen Subventionierung von Industriestrom – im Wesentlichen die Möglichkeit, erneuerbaren Strom durch eine starke Ausweitung des Angebots zu verbilligen.
5 Schlussfolgerungen und Handlungsfelder
Die Transformation der energieintensiven Grundstoffindustrie hin zu Klimaneutralität ist technisch und wirtschaftlich voraussetzungsreich und für die produzierenden Unternehmen, die häufig in einem starken internationalen Wettbewerb stehen, mit hohen Risiken verbunden. Die Unternehmen werden die Transformation daher nicht alleine stemmen können. Daraus leitet sich für die Politik die Aufgabe ab, die Unternehmen beim notwendigen Umbauprozess zu unterstützen.
Zur staatlichen Unterstützung der industriellen Transformation existiert bereits ein breites Angebot an forschungs- und industriepolitischen Instrumenten. Es umfasst u. a. Fördermechanismen zur Steigerung der Energieeffizienz (z. B. die »Bundesförderung für Energie- und Ressourceneffizienz in der Wirtschaft«), für den Aufbau emissionsarmer bzw. -freier Prozesstechnologien (z. B. das Förderprogramm »Dekarbonisierung in der Industrie«) oder für die Etablierung einer Wasserstoffwirtschaft (z. B. die »Technologieoffensive Wasserstoff«). Weitere nationale Maßnahmen stehen kurz vor der Einführung bzw. sind geplant, wie z. B. die Maßnahmen des Wachstumschancengesetzes 9 zur Verbesserung der steuerlichen Rahmenbedingung für Klimainvestitionen oder das »Förderprogramm Klimaschutzverträge« (Stand Dezember 2023).10 Hinzu kommen Maßnahmen auf europäischer Ebene, etwa die schrittweise Einführung des CO2-Grenzausgleichssystems für Produkte der Eisen, Stahl- und Zementindustrie.
Eine Analyse der Effekte und Erfolgschancen der bereits umgesetzten und angekündigten politischen Instrumente, die in komplexer Weise miteinander wechselwirken, konnte im Rahmen des TA-Projekts nicht geleistet werden. Im Folgenden richtet sich das Augenmerk auf die Bedingungen und Anforderungen, die für ein Gelingen der Transformation in den drei hier behandelten Grundstoffindustrien als maßgeblich angesehen werden. Als Basis für die Ausführungen dienten Inhalte des Gutachtens von Prognos und Wuppertal Institut, die erweitert und aktualisiert wurden.
5.1 Politische Handlungsoptionen zur Förderung der Transformation
Für die in diesem TA-Projekt untersuchten Grundstoffindustrien Eisen/Stahl, Zement und HVC zeigen die Analysen ein facettenreiches Bild in Bezug auf die Transformation. Für die Politik bestehen entsprechend vielfältige Möglichkeiten, den Umbauprozess zu unterstützen.
Technische Realisierungsbedingungen durch gezielte Forschungs- und Entwicklungsförderung verbessern
Die Transformation der betrachteten Grundstoffindustrien wird als technisch machbar angesehen. Für eine Reihe von emissionsarmen alternativen Produktionsprozessen existiert technologisches Basiswissen und es liegen Erfahrungswerte aus anderen Produktionsbereichen vor (z. B. Einsatz von EAF für die Primärstahlerzeugung). Weitere Technologieoptionen haben Test- und Zulassungsverfahren erfolgreich überwunden (z. B. neue Normzemente) oder werden derzeit in Pilotanlagen erprobt (z. B. die reine wasserstoffbasierte Direktreduktion von Eisenerz). Die industrielle Umsetzung hat aber gerade erst begonnen und ein großskaliger Einsatz ist noch nicht erreicht. Auf dem Weg dahin sind noch viele technische Detailfragen zu klären und verfahrenstechnische Herausforderungen zu meistern.
Für die Unternehmen der Grundstoffindustrie, aber auch z. B. für den Maschinen- und Anlagenbau ist die Transformation daher mit einem hohen Aufwand für Forschung und Entwicklung verbunden. Politische Möglichkeiten, um die Unternehmen in dieser Hinsicht zu entlasten, sind ein Ausbau der projektbezogenen Forschungs- und Entwicklungsförderung, die Ausweitung der steuerlichen Forschungsförderung oder die Förderung von Pilot- und Demonstrationsvorhaben. Im Rahmen dieses TA-Projekts identifizierte wichtige technologische Fragestellungen für eine gezielte Forschungs- und Entwicklungsförderung werden in Kapitel 5.2 gebündelt dargestellt und begründet.
Die verfügbaren klimafreundlichen Technologieoptionen erscheinen teilweise wechselseitig exklusiv. Daher müssen Unternehmen zu bestimmten Zeitpunkten im Transformationsprozess Pfadentscheidungen für gewisse Technologieoptionen treffen. Diese Unternehmensentscheidungen sollten in der Forschungs- und Entwicklungsförderung Berücksichtigung finden, da ab diesem Zeitpunkt auf diese Technologieoptionen fokussierte Förderprogramme eine höhere Wirkung entfalten dürften als technologieoffen formulierte Programme.
Integratives Gesamtkonzept für die Förderung
Zwischen den betrachteten Grundstoffindustrien bestehen Wechselwirkungen, sodass sich der Technologiewechsel in einer Grundstoffindustrie auf die Rahmenbedingungen der Transformation in den anderen Grundstoffindustrien auswirkt. Dies betrifft etwa die Verfügbarkeit der begrenzt verfügbaren grünen Energieträger oder Rohstoffe, um welche die Grundstoffindustrien untereinander, aber auch mit anderen Sektoren (Gebäude, Verkehr) konkurrieren. Außerdem werden die Energie- und Stoffströme zwischen den Grundstoffindustrien beeinflusst. Ein Beispiel ist Hüttensand aus dem Hochofen, der eine kritische Ressource für die Zementindustrie darstellt, die bei einer weitgehenden Umstellung auf das Direktreduktionsverfahren wegzubrechen droht. Es könnte daher sinnvoll sein, einen Teil der Hochöfen mit CO2-Abscheidung weiter zu betreiben. Gleichzeitig können neue Stoffflüsse entstehen, wie z. B. die Belieferung der HVC-Produktion mit CO2 aus der Abscheidung bei Zementwerken.
Wechselwirkungen bestehen auch zu anderen Branchen entlang der Wertschöpfungskette: Vom notwendigen Umbauprozess könnte vor allem der deutsche Maschinen- und Anlagenbau stark profitieren, sofern hier rechtzeitig ausreichende Kapazitäten für diese Aufgabe aufgebaut werden. Synergien zum Energiesektor könnten dann geschaffen werden, wenn unter den verfügbaren Technologieoptionen vor allem solche ausgewählt werden, die grundsätzlich einen flexiblen Betrieb erlauben und so die Einbindung fluktuierender erneuerbarer Energien in das Stromsystem unterstützen könnten. Um künftig eine gesicherte inländische Nachfrage nach grünen Grundstoffen zu schaffen, müssen schließlich auch die nachgelagerten Wertschöpfungsketten in den strategischen Überlegungen Berücksichtigung finden. Hier gilt es, die Innovations- und Wettbewerbsfähigkeit der Abnehmerbranchen zu erhalten, wobei hier vor allem kleine und mittlere Unternehmen (KMU) im verarbeitenden Gewerbe eine bedeutende Rolle spielen, die auf ihren Gebieten nicht selten Weltmarktführer sind.
Aufgrund der starken Wechselwirkungen innerhalb und zwischen den Branchen sind integrative Förderprogramme, die nicht nur einzelne Industrien adressieren, sondern die Transformation als branchen- und sektorübergreifende Aufgabe verstehen und alle Stufen der Wertschöpfungskette miteinbeziehen, ein wichtiger Erfolgsfaktor für das Gelingen der Transformation. Dazu wären in einem ersten Schritt ein intensiverer Austausch zwischen allen relevanten Akteuren (einschließlich KMU) nötig. Diesen Dialog gilt es zu organisieren, um aus den dabei gewonnenen Erkenntnissen in einem zweiten Schritt zwischen den Branchen und Sektoren abgestimmte Strategien und politische Unterstützungskonzepte zur Beförderung der Transformation ableiten zu können.
Sicherung grüner Ressourcen
Eine ausreichende Verfügbarkeit von grünen Ressourcen, wie erneuerbarer Strom, grüner Wasserstoff, Biomasse oder Pyrolyseöl aus dem chemischen Recycling, ist für das Gelingen der Transformation essenziell. Dazu notwendig sind neben einer höheren Ressourceneffizienz die Ausweitung der erneuerbaren Energien in Deutschland, der Aufbau einer heimischen Wasserstoffindustrie und die Stärkung der Kreislaufwirtschaft. Politische Unterstützungsinstrumente, wie z. B. die vielfältigen Maßnahmen zur Förderung des Ausbaus der erneuerbaren Stromerzeugung, die vorgesehene Förderung von Elektrolyseuren in Deutschland oder die geplante nationale Kreislaufwirtschaftsstrategie, weisen hier den richtigen Weg. Trotz großer Anstrengungen zur Erweiterung des heimischen Angebots ist jedoch davon auszugehen, dass ein beträchtlicher Teil der künftig benötigten grünen Ressourcen (z. B. Wasserstoff, Naphtha, Methanol) auch importiert werden müssen.11 Hier gilt es, Energiepartnerschaften mit möglichen Exportländern weiter auszubauen und wirtschaftliche Kooperationen zwischen diesen Ländern und Unternehmen in Deutschland für einen kostengünstigen Import von grünen Energieträgern und Rohstoffen zu unterstützen.
Die Wirkungen bzw. Erfolge der bestehenden und künftig geplanten politischen Instrumente zur Sicherung grüner Ressourcen sollten (gemessen daran, ob die tatsächlichen bzw. erwarteten Bedarfe laufend gedeckt werden können) regelmäßig evaluiert werden, um nötigenfalls frühzeitig nachsteuern zu können. Beim Aufbau neuer Importnetzwerke scheint es zudem sinnvoll, auf eine hinreichende Diversifizierung zu achten, um Importabhängigkeiten zu einzelnen Lieferländern zu vermeiden. Im Rahmen von konkreten Abkommen erscheint es schließlich wichtig, dass neben technischen und ökonomischen Aspekten auch soziale, ökologische und (geo)politische Faktoren von Beginn an angemessene Berücksichtigung finden, um die Liefersicherheit auch längerfristig gewährleisten zu können.12
Investitionen in klimaneutrale Produktionsprozesse anreizen
Emissionsarme Produktionsprozesse gehen im Vergleich mit konventionellen Technologien meist mit höheren Investitions- und Betriebskosten einher, was zu (temporär) höheren Produktionskosten führt. Die Kostenparität (vor allem infolge steigender Kosten für CO2-Emissionszertifikate) wird gemäß den in diesem TA-Projekt durchgeführten Modellrechnungen für die Stahlproduktion um 2035 und für die Zementherstellung um 2030 erwartet, anschließend dürften die klimafreundlichen Produktionsrouten günstiger sein. Eine emissionsarme Herstellung von HVC bleibt den Berechnungen zufolge allerdings auch über 2045 hinaus erheblich teurer als mit konventionellen Verfahren.
Aufgrund der (temporär) höheren Produktionskosten sind Investitionen in klimafreundliche Produktionsprozesse im derzeitigen Wettbewerbsumfeld wirtschaftlich unattraktiv. Um schon jetzt, also noch bevor die Kostenparität erreicht wird, Investitionen anzureizen, sind staatliche Förderprogramme zur Kompensation der klimaschutzbedingten Mehrkosten sinnvoll. Ein Beispiel dafür ist das neu aufgelegte Förderprogramm für Klimaschutzverträge des BMWK, durch welches die Zusatzkosten einer emissionsarmen Produktion durch den Staat ausgeglichen werden sollen. Angesichts der teilweise hohen Kostendifferenzen zwischen den klimafreundlichen und konventionellen Produktionsrouten ist es wichtig, entsprechende Förderprogramme mit ausreichend hohen Mitteln auszustatten. Sollten beihilferechtliche Restriktionen das erforderliche Fördervolumen limitieren, müsste auf Ebene der EU eine Harmonisierung in Bezug auf entsprechend große Pakete angestrebt werden.
Vor allem für die HVC-Produktion fehlt es auch langfristig an ökonomischen Anreizen für Klimaschutzinvestitionen. Um den Preis für grünes HVC nicht dauerhaft durch staatliche Subventionen drücken zu müssen, sind zusätzliche Instrumente, wie etwa die Etablierung grüner Märkte, erforderlich.
Grüne Märkte für Endprodukte anregen
Die (temporär) höheren Produktionskosten für klimafreundliche Grundstoffe führen – sofern die Mehrkosten nicht staatlich kompensiert, sondern entlang der Wertschöpfungskette weitergegeben werden – zu höheren Preisen bei Endprodukten (Autos, Gebäude, Medikamente etc.). Das Ausmaß der Kostensteigerungen lässt sich derzeit nicht verlässlich quantifizieren. Gemäß den in diesem TA-Projekt durchgeführten vereinfachenden Modellrechnungen wirken sich die Kostensteigerungen bei den Grundstoffen jedoch wohl nur marginal auf die Preise der Endprodukte aus. Bestätigt sich dies, könnte die Schaffung grüner Märkte auf Ebene der Endprodukte eine große Hebelwirkung entfalten, da sich so eine Nachfrage für die teureren klimafreundlichen Grundstoffe praktisch ohne finanziellen Mehraufwand für die Käufer der Endprodukte generieren ließe. Dies erscheint vor allem für die HVC-Produktion attraktiv, um eine dauerhafte staatliche Subventionierung der grünen Produktion zu vermeiden.
Die Etablierung grüner Märkte für Endprodukte erfordert Transparenz über die Eigenschaften der grünen Vorprodukte, was durch Standardisierung und Normierung erreichbar ist. Parallel dazu erscheint die Schaffung grüner Finanzierungsinstrumente hilfreich, um einen privatwirtschaftlichen Finanzierungsmarkt für Klimainvestitionen aufzubauen. Dafür wären zeitnah die notwendigen Rahmenbedingungen zu setzen. Auf nationaler Ebene können grüne Märkte für Endprodukte über die öffentliche Beschaffung gestärkt werden: Durch eine umweltfreundliche öffentliche Beschaffung (z. B. im Fahrzeugpark der öffentlichen Hand) wird einerseits eine konstante Nachfrage erzeugt, andererseits kann dies Vorbildcharakter für andere Kundengruppen (Privatwirtschaft, Haushalte) haben.
Internationalen Wettbewerb für Grundstoffe adressieren
Weil Klimaschutz mit höheren Kosten verbunden ist, können Produktionsverlagerungen in Weltregionen, in denen weiterhin kostengünstig mit konventioneller Technologie produziert werden kann, aus heutiger Sicht nicht ausgeschlossen werden (Carbon Leakage).
Die Einführung eines europäischen CO2-Grenzausgleichsystems für Erzeugnisse der Eisen/Stahl- und Zementindustrie (bisher allerdings noch nicht für HVC) stellt voraussichtlich ein effizientes Instrument dar, um zumindest für den europäischen Markt die Risiken für Produktionsverlagerungen zu verringern. Bisher fehlt es jedoch an einer Lösung für die außereuropäischen Märkte. Sollte es aufgrund von handelsrechtlichen Regelungen auch künftig nicht möglich sein, die klimaschutzbedingten Mehrkosten bei Exporten europäischer Grundstoffe staatlich zu kompensieren, müssen die internationalen Abstimmungen und Harmonisierungen der Klimaschutzanstrengungen in den globalen Grundstoffindustrien vorgetrieben werden. Dies umfasst u. a. die folgenden ambitionierten Aufgabenfelder: Einheitliche Klimaziele, Harmonisierung von Bilanzierungs-, Anrechnungs- und Zertifizierungssystemen, Erweiterung von Emissionshandelssystemen, Angleichung von CO2-Kosten und -Steuern, Etablierung internationaler grüner Märkte mit harmonisierten Anforderungen sowie Erschließung und Anrechnung von globalen CO2-Senken. Der Weg dahin ist aber noch weit.
Standortvorteile in Deutschland stärken
Eine Gefahr für Produktionsverlagerungen entsteht auch aus dem Umstand, dass grüne Energieträger und Rohstoffe in anderen Teilen der Welt deutlich kostengünstiger erzeugt werden können als in Deutschland (Green Leakage).
Politische Handlungsoptionen gegen Green Leakage bestehen in erster Linie im konsequenten Ausbau der erneuerbaren Energien mitsamt den notwendigen Infrastrukturen in Deutschland, um das Angebot zu erhöhen und damit den Preis für grüne Energieträger zu senken. Parallel dazu können Energiepartnerschaften mit möglichen Exportländern ausgebaut werden. Fraglich bleibt allerdings, ob diese Instrumente ausreichen, um den Wettbewerbsnachteil hinsichtlich der Energiekosten vollständig auszugleichen.
Bei Standortentscheidungen der Unternehmen sind die Energiekosten aber nur ein Faktor von vielen. Weitere wichtige Standortfaktoren sind z. B. die Innovationsfähigkeit, die Verfügbarkeit von Fachkräften, die Kundennähe, eine hohe Rechtssicherheit, ein gutes Infrastrukturangebot oder die Zuverlässigkeit der Energieversorgung. In Bezug auf diese Faktoren sind Deutschland und Europa gegenüber vielen Ländern der Welt im Vorteil. Politische Anstrengungen zum Erhalt und zur Stärkung dieser Standortfaktoren erscheinen daher sinnvoll, um mögliche Nachteile durch hohe Energiekosten zu kompensieren und so das Risiko für Green Leakage zu senken. Mit Blick auf die Grundstoffindustrien sollten diese Anstrengungen einem integrativen Ansatz folgen, der auch auf eine Stärkung der nachgelagerten Wertschöpfungsstufen abzielt, um so die Nachfrage nach Grundstoffen zu sichern sowie bestehende Standortvorteile durch Kundennähe und vertikale Integration beizubehalten bzw. zu stärken.
Transformation nicht durch einen Fachkräftemangel abbremsen
Die Transformation geht mit Veränderungen in den benötigten beruflichen Qualifikationen der Beschäftigten einher. Für die in diesem TA-Projekt betrachteten Grundstoffindustrien werden zwar keine grundlegend anderen Berufsbilder bzw. Ausbildungen für nötig erachtet, allerdings besteht ein Bedarf an Zusatzqualifikationen. Zudem erhöhen die mit neuen Anlagen einhergehende Digitalisierung und Automatisierung die Anforderungen an die Beschäftigten.
Derzeit ist das Wissen darüber, welche beruflichen Qualifikationen künftig weiterhin bzw. zusätzlich erforderlich sind, noch lückenhaft. Ein besseres Verständnis ist nötig, um entsprechende Anpassungen in der beruflichen Aus- und Weiterbildung sowie in der akademischen Bildung vorzunehmen. Handlungsdruck besteht insbesondere in der Stahlindustrie, da hier der Technologiewechsel bereits in den kommenden Jahren ansteht (die Zement- und HVC-Produktion sind diesbezüglich weniger zeitkritisch). Anderenfalls besteht die Gefahr, dass die Transformation durch einen Mangel an qualifizierten Mitarbeiterinnen und Mitarbeitern ausgebremst wird.
Rahmenbedingungen für die Realisierung von CCS/CCU verbessern
Für eine klimaneutrale Stahl- und HVC-Produktion bis 2045 ist die CO2-Abscheidung eine gangbare Technologieoption, für eine klimaneutrale Zementproduktion ist sie aus heutiger Sicht alternativlos. Das Kohlendioxid-Speicherungsgesetz (KSpG)13 von 2012 erlaubt in Deutschland bislang nur Demonstrationsprojekte und beschränkt die inländische Gesamtspeichermenge. In einigen europäischen Ländern (vor allem Nordseeanrainer) und außerhalb Europas wird die CO2-Speicherung zum Teil schon im industriellen Maßstab eingesetzt. Abgeschiedenes CO2 aus Deutschland könnte künftig z. B. nach Norwegen transportiert und dort unter dem Meeresboden eingelagert werden. Dafür erforderlich wäre eine leistungsfähige CO2-Transportinfrastruktur (vor allem Pipelines), um die Industrieanlagen mit den Speicherstätten zu verbinden. Sollte darüber hinaus in Deutschland abgeschiedenes CO2 nicht nur exportiert, sondern auch hierzulande in großen Mengen gespeichert werden, so wäre ein entsprechender Rechtsrahmen zu schaffen. Allerdings ist bei einer inländischen Speicherung mit gesellschaftlichen Akzeptanzproblemen zu rechnen.
Da in der Stahlindustrie Entscheidungen über einen möglichen Weiterbetrieb von (dann mit CO2-Abscheidung ausgerüsteten) Hochöfen zeitnah erfolgen müssen und es eine klimafreundliche Zementindustrie in Deutschland nur mit CO2-Abscheidung geben wird, sind angesichts der zu erwartenden langen Vorlaufzeiten rasche politische Entscheidungen zum Aufbau einer leistungsfähigen CO2-Transportinfrastruktur und gegebenenfalls großskaligen Speicherstätten in Deutschland erforderlich. An diese Entscheidungen anschließende Förderprogramme wären dann gezielt danach auszurichten, bestehende Wissenslücken zu schließen, die Akzeptanz zu fördern und den Aufbau der notwendigen Infrastrukturen zu beschleunigen.
Planungssicherheit durch langfristige politische Rahmensetzung
Die bisher geschnürten Instrumentenpakete zur staatlichen Unterstützung der Transformation decken i. d. R. den Zeitraum bis (maximal) 2030 ab. Dies gilt teilweise auch für aktuell geplante Maßnahmen, wie das Wachstumschancengesetz oder die Senkung der Stromsteuer für das produzierende Gewerbe auf den europäischen Mindestsatz (Stand November 2023). Bei der Transformation der Grundstoffindustrie handelt es sich jedoch um einen langfristigen Umbauprozess, der teilweise bis weit in die 2040er Jahre reichen wird. Aufgrund der langen Investitionszyklen bei Anlagen sind die Unternehmen bereits heute gezwungen, bedeutende Planungs- und Investitionsentscheidungen über den gesamten Zeitraum bis 2045 zu treffen. Es ist folglich wichtig, der Grundstoffindustrie zeitnah eine möglichst große Klarheit über die zukünftigen Rahmenbedingungen für die industrielle Produktion weit über 2030 hinaus zu geben. Mit der Einführung eines europäischen CO2-Grenzausgleichssystems, den Regelungen für den Start eines Wasserstoffkernnetzes im novellierten Energiewirtschaftsgesetz (EnWG)14 und der geplanten Einführung von Klimaschutzverträgen (für die eine Laufzeit von jeweils 15 Jahren vorgesehen ist) wurden erste Maßnahmen verabschiedet, die diesem Anspruch gerecht werden. Weitere politische Entscheidungen über die Rahmenbedingungen für die Grundstoffproduktion in Deutschland nach 2030 sollten folgen.
Zusätzlich zu konkreten politischen Maßnahmen zur Schaffung klarer Rahmenbedingungen ist schließlich ein glaubwürdiges Bekenntnis der Politik wichtig, die Grundstoffindustrie in Deutschland halten zu wollen und sie bei der anstehenden Transformation zu unterstützen. Die im Herbst 2023 vorgelegte Industriestrategie des BMWK ist dafür ein Beispiel.
5.2 Schwerpunkte für die Forschung und Entwicklung
Im Folgenden werden identifizierte Fragen für die Forschung und Entwicklung gebündelt dargestellt und begründet.
5.2.1 Technologische Fragestellungen
Unternehmen der Grundstoffindustrie haben die Notwendigkeit eines klimafreundlichen Umbaus ihrer Produktionsprozesse und -anlagen erkannt und die notwendigen Schritte dazu vielfach auch bereits in entsprechenden Transformationsstrategien konkretisiert. Bisher existieren diese Strategien aber meist nur auf dem Papier. Die technologische Umsetzung stellt die Unternehmen vor große Herausforderungen, weil es sich um eine »Operation am offenen Herzen« handelt, die unter hohem Zeit- und Wettbewerbsdruck stattfindet. So wird es, um die Kontinuität der Produktion aufrechtzuerhalten, nötig sein, den Technologiewechsel größtenteils bei laufender Produktion zu realisieren (was gegebenenfalls temporär parallele Produktionsstrukturen erforderlich macht). Zudem müssen die neuen Produktionsprozesse mit ihren spezifischen Energie- und Stoffströmen, Produktqualitäten und -quantitäten möglichst nahtlos in ein bestehendes, hochkomplexes und hocheffizientes industrielles Gefüge sowie in bestehende Kundennetzwerke eingefügt werden. Ob bzw. wie dies mit den verfügbaren Technologieoptionen gelingen kann, ist noch nicht hinreichend geklärt und muss weiter erforscht und erprobt werden. Dabei gilt: Je mehr technisches Wissen über die möglichen Vermeidungstechnologien zur Verfügung steht, desto reibungsloser bzw. vorausschauender lässt sich der Umbauprozess gestalten.
Eisen/Stahl
Im international wettbewerbsintensiven Stahlmarkt hat sich die deutsche Stahlindustrie bislang vor allem durch ihre technische Kompetenz in der Rohstahlherstellung und somit durch die Produktion von hochqualitativen und innovativen Stahlsorten für besonders anspruchsvolle Abnehmerbranchen (z. B. Automobil, Maschinenbau, Bauindustrie) behaupten können. Durch die Transformation dürfen diese Wettbewerbsvorteile sowie bestehende Kundennetzwerke nicht gefährdet werden. In Bezug auf die emissionsarmen Technologieoptionen lassen sich daraus folgende Schwerpunkte für die Forschung ableiten.
Welche Stahlqualitäten können mit den klimafreundlichen Produktionsprozessen kommerziell hergestellt werden?
Die höchsten Stahlqualitäten werden gegenwärtig im Hochofen und der angeschlossenen Konvertermetallurgie der Primärstahlerzeugung erzielt. Falls die konventionelle Hochofenroute weitgehend durch die Route wasserstoffbasierte Direktreduktion mit Lichtbogenofen, die ohne Konverter auskommt, ersetzt wird, könnten bestimmte hochwertige Stähle mit niedrigen Kohlenstoff- und Stickstoffgehalten zur Herausforderung werden, die im Lichtbogenofen nicht ohne weiteres erzeugt werden können. Die notwendigen nachgeschalteten Behandlungsschritte erhöhen den technologischen Aufwand, was die Produktionskosten erhöht und die Produktivität verringert. Außerdem besteht ein Zielkonflikt zwischen der erzielbaren Stahlqualität und der Wirtschaftlichkeit des Lichtbogenofens: Durch Zugabe von Eisen- und Stahlschrott kann die Produktivität des Ofens gesteigert werden, allerdings geht dies aufgrund der Verunreinigungen im Schrott zulasten der Stahlqualität. Weitere Forschung und Entwicklung ist notwendig, um optimale Prozessbedingungen für diese Route zu identifizieren.
In Bezug auf die Stahlqualitäten scheint aus heutiger Sicht die Route wasserstoffbasierte Direktreduktion mit Schmelzofen und Konverter besser geeignet zu sein, da hier die bestehende Konvertermetallurgie bestehen bleibt. Der Einsatz von elektrischen Schmelzöfen für die Herstellung von reinem Roheisen ist allerdings noch kein etabliertes Verfahren und muss zunächst erprobt und gegebenenfalls angepasst werden.
Wie lassen sich klimafreundliche Produktionsprozesse möglichst nahtlos in bestehenden Produktionsstrukturen einbinden?
Im Stahlwerk ist die gesamte Logistik auf die Produktivität der Gießanlagen ausgerichtet, damit der Produktionsprozess vom Eisenerz bis zur Stahlbramme kontinuierlich und optimal ausgelastet abläuft. Gegenüber dem Konverter haben heute gängige Lichtbogenöfen aber einen geringeren Durchsatz, sodass durch den Technologiewechsel die Mengenflüsse und zeitlichen Abläufe im Stahlwerk gestört werden können. Wenn parallel betriebene Lichtbogenöfen vermieden werden sollen (wodurch sich die Komplexität der Gesamtlogistik erhöhen würde), ist eine Weiterentwicklung der Anlagentechnik des Lichtbogenofens nötig.
Dahingegen bewirkt die Route mit Schmelzofen hinsichtlich der Kapazitäten keine Restriktionen. Probleme bereitet hier jedoch der Übergang vom Schmelzofen zum Konverter. In der konventionellen Hochofenroute nutzt der Konverter im Roheisen enthaltenen Kohlenstoff als Energielieferant, welcher im wasserstoffreduzierten Roheisen aber fehlt. Der Kohlenstoff muss daher im Schmelzofen zugesetzt werden, was hier aber den Energiebedarf erhöht und zu unerwünschten CO2-Emissionen führt. Notwendig sind alternative Ansätze für die Energiezufuhr im Konverter, was weitere Forschung erfordert.
Wie kann Deutschlands Innovationskraft im Bereich Stahl erhalten und gestärkt werden?
Die Stahlindustrie hat als Basisindustrie eine zentrale Funktion für viele deutsche Wertschöpfungsketten. Bedeutende Sektoren wie die Automobilindustrie, der Maschinen- und Anlagenbau oder die elektrotechnische Industrie sind auf ein kontinuierliches Angebot an innovativen und hochwertigen Stählen angewiesen.
Die Stahl- und Stahlanwendungsforschung in Deutschland stützt sich auf ein dichtes Netz von Forschungseinrichtungen und Hochschulen. Diese Forschung wird überwiegend aus Mitteln der großen Stahlunternehmen finanziert. Dies hat u. a. zur Folge, dass in der Wertschöpfungskette nachfolgende KMU nur im geringen Maße mit ihren Potenzialen in die Forschung integriert sind. Diese KMU haben jedoch das Potenzial, z. B. im Bereich erneuerbare Energien in Verbindung mit innovativen Stahlanwendungen eine Vorreiterrolle zu übernehmen. Ansätze zur besseren Einbindung von KMU existieren. Zum Beispiel unterstützt das Stahlinstitut VDEh mit seinem Betriebsforschungsinstitut die Zuse-Gemeinschaft, welche die Interessen der unabhängigen privatwirtschaftlich organisierten Forschungseinrichtungen vertritt. Solche Aktivitäten könnten durch die Politik unterstützt und so weiter ausgebaut werden.
Zement
Die THG-Emissionen der Zementindustrie gehen zu zwei Dritteln auf die Klinkerproduktion zurück. Da aus heutiger Perspektive bis 2045 keine massentaugliche Alternative zum Klinker existiert, hat die Zementindustrie – um den künftigen Bedarf an CO2-Abscheidung soweit wie möglich zu senken – die Entwicklung klinkerarmer Normzemente forciert. Deren Leistungsfähigkeit hängt aber im hohen Maße von den als Klinkerersatz verwendeten Zumahlstoffen ab. Das zu erwartende Wegbrechen von etablierten Zumahlstoffen wie Hüttensand und Steinkohlenflugasche stellt daher eine große Herausforderung für die Zementindustrie dar. Verschärft wird die Problematik durch die anwenderseitig stetig steigenden Anforderungen an moderne Betonanwendungen (z. B. Carbonbeton, Leichtbeton, Ultrahochfestbeton, Beton für den 3-D-Druck). Mit Blick auf die Forschungs- und Entwicklungsförderung können daraus die im Folgenden angeführten Schlussfolgerungen gezogen werden.
Eignen sich alternative Schlacken für Hüttensand?
Durch die Transformation der Stahlindustrie weg von Hochofen hin zur Direktreduktion wird die Verfügbarkeit von Hüttensand stark reduziert. Eine wichtige Forschungsfrage lautet daher, ob bzw. unter welchen Bedingungen die nach dem Technologiewechsel anfallenden Schlacken (Lichtbogenofen-, Schmelzofen- oder Konverterschlacke) geeignet sind, als adäquater Ersatz für Hochofenschlacke in der Zementindustrie eingesetzt zu werden.
Alternative Zumahlstoffe finden
Auf der Suche nach neuen Zumahlstoffen werden einige Hoffnungen in Tonminerale gesetzt, die in der Natur in großen Mengen vorkommen. Die Heterogenität dieser Tongemische stellt allerdings eine große Herausforderung dar, da damit hergestellte Zemente je nach Lagerstätte der Tonminerale ggf. unterschiedliche Eigenschaften aufweisen könnten. Der Forschungsbedarf für eine notwendige Erweiterung des Portfolios an geeigneten Zumahlstoffen ist daher aktuell hoch.
Forschung zu neuen Bindemittelsystemen verstärken
Um jenseits der CO2-Abscheidung größere Emissionsminderungen in der Zementindustrie zu realisieren, sind neue leistungsfähige Bindemittelsysteme nötig, die nicht auf Klinker beruhen. An diesen wird schon seit Jahrzehnten geforscht, allerdings ohne, dass bislang ein Durchbruch zu einer breiten Anwendbarkeit gelungen ist. Ein Grund hierfür ist die zu geringe, in ihrem Budget begrenzte Forschungsintensität zu dieser komplexen Materie. Entsprechende Forschungsanstrengungen könnten daher durch gezielte und langfristig angelegte Förderprogramme intensiviert werden.
Bestehende Innovationshemmnisse senken
Der Markteintritt für neue Bindemittelsysteme wird vor allem auch durch die aufwändigen und zeitintensiven Zulassungsverfahren erschwert. In den letzten 20 Jahren wurden wissenschaftsbasierte Ansätze und aufwendige Untersuchungsmethoden entwickelt, um die Prozesse der Bindemittelchemie insbesondere auch in Bezug auf die Dauerhaftigkeit besser zu verstehen. Die Modellierung chemischer Reaktionen am Computer spielt ebenfalls eine wichtige Rolle, um das Verhalten von Bindemitteln in unterschiedlichen Situationen über mehrere Jahre besser vorherzusagen. Diese Grundlagenforschung hilft, die Innovationszyklen zu beschleunigen. Ein Ausbau der Grundlagenforschung in der Bindemittelchemie könnte daher dazu beitragen, innovative Bindemittel schneller auf den Markt zu bringen.
Innovative kleine Unternehmen und Institutionen fördern
Auffallend ist, dass die Patentportfolios kleiner Unternehmen und Institutionen, die zumeist außerhalb der Zementbranche angesiedelt sind, eine wichtige Rolle bei Innovationen im Zementbereich spielen. Von großen Unternehmen wurden eigene Investitionen für Forschung und Entwicklung in gänzlich neue Bindemittelsysteme bisher nicht getätigt. Ein Grund könnten die langen Zeithorizonte und damit einhergehende Risiken bei der Entwicklung und Zulassung sein. Die Förderung radikal neuer Forschungsansätze bei kleinen innovativen Unternehmen oder Institutionen könnte somit ein großer Hebel sein, um bei großen Zementherstellern Interesse zu wecken und Investitionen auszulösen.
HVC
Die Umstellung der Produktionsprozesse gilt hier – verglichen mit den anderen betrachteten Grundstoffindustrien – als weniger voraussetzungsreich, auch wenn noch technische Detailfragen zu klären sind. Offene Fragen bestehen hingegen in Bezug auf die Umstellung von fossilen auf grüne Rohstoffe. So hängen die Realisierungsbedingungen für die Transformation der HVC-Produktion insbesondere davon ab, ob bzw. wie die erforderlichen Mengen an grünen Rohstoffen bereitgestellt werden können.
Alternative Technologieoptionen weiterentwickeln
Beim elektrischen Steamcracker stellt die hohe Wärmeübertragung auf kleinem Raum eine technische Herausforderung dar. Hier bestehen noch offene Forschungs- und Entwicklungsfragen in Bezug auf geeignete Beheizungsarten, Materialien und Stromübertragungstechniken. Anlagen zur Herstellung von Olefinen aus Methanol werden z. B. in China bereits großtechnisch eingesetzt. Um künftig auch Aromaten über diese Route synthetisieren zu können, besteht aber noch weiterer Forschungs- und Entwicklungsbedarf. In Bezug auf den Einsatz von Pyrolyseöl im Steamcracker müssen noch optimale Verwertungswege für die anfallenden Nebenprodukte und Reststoffe gefunden werden. Denkbar ist eine stoffliche Weiterverwendung, eine Rückführung als Rohstoff in Vergasungs- und Reformierungsprozesse oder eine thermische Nutzung.
Verfügbarkeit der Ressourcen für alternative Routen klären
Eine klimafreundliche HVC-Produktion ist über unterschiedliche Routen und mit verschiedenen grünen Rohstoffen (Pyrolyseöl, synthetisches Naphtha, grünes Methanol) möglich. Die Rohstoffe wiederum können über verschiedene Synthesewege aus unterschiedlichen Ausgangsstoffen (Altkunststoffe, Biomasse, Wasserstoff, CO2) gewonnen werden. Abschätzungen zu den langfristigen Mengenpotenzialen für diese Ausgangsstoffe sind aber noch mit hohen Unsicherheiten verbunden, außerdem konkurrieren auch andere Branchen und Sektoren um diese knappen Ressourcen. Um den Unternehmen der HVC-Produktion Investitionsentscheidungen für bestimmte Routen und Synthesewege zu erleichtern, ist frühzeitig eine möglichst hohe Klarheit über künftig verfügbare Mengen und Preise für diese Ressourcen nötig. Zu diesem Zweck sollten Untersuchungen zu den langfristigen nachhaltigen Mengenpotenzialen für diese Ausgangsstoffe sowie zu integrierten Nutzungsszenarien unter Einbezug aller Nachfragebranchen fortgeführt und ggf. intensiviert werden.
Forschungsfragen zum chemischen Recycling
Soll die Herstellung von HVC aus Pyrolyseölen aus dem chemischen Recycling forciert werden, so sind neben ausreichenden Mengen an Altkunststoff auch großtechnische Pyrolyseanlagen nötig. Zwar sind Pyrolyseanlagen für Altkunststoff bereits am Markt, in Bezug auf eine Hochskalierung bestehen aber noch offene Forschungsfragen. Dies betrifft z. B. ökologische Fragen, etwa hinsichtlich der Beseitigung von problematischen Rückständen. Außerdem wären die Auswirkungen auf andere Nutzungsarten für Altkunststoffe zu untersuchen, etwa auf das stoffliche Recycling oder die thermische Verwertung zur Fernwärmeerzeugung in Müllverbrennungsanlagen, um optimale Verwertungsstrategien für Altkunststoffe zu entwickeln und auf diese Weise ihren Beitrag zur Kreislaufwirtschaft zu maximieren.
5.2.2 Ökonomische und sozioökonomische Forschungsfragen
Klar ist, dass die Transformation der Stahl-, Zement- und HVC-Produktion hin zu (weitgehender) Klimaneutralität nicht ohne teilweise massive Auswirkungen vonstattengehen wird. Diese betreffen sozioökonomische Faktoren (z. B. Produktionskosten, Wettbewerbsfähigkeit, Beschäftigung, Qualifikationen) in den Grundstoffindustrien selbst, aber auch darüber hinaus auf vor- (z. B. auf den Maschinen- und Anlagenbau) und nachgelagerte Branchen (z. B. Automobil, Bauwirtschaft) Über das genaue Ausmaß dieser Wirkungen sind gegenwärtig meist nur Mutmaßungen möglich, da fundierte Untersuchungen bislang weitgehend fehlen. Belastbare Erkenntnisse zu möglichen sozioökonomischen Effekten unterschiedlicher Transformationspfade sind aber wichtig, um den Umbauprozess proaktiv zu gestalten. In diesem TA-Projekt identifizierte offene Forschungsfragen könnten u. a. durch folgende Forschungsaktivitäten adressiert werden.
Wie wirken sich teurere Grundstoffe auf die Preise für Endprodukte aus?
Gemäß den für den vorliegenden Bericht durchgeführten Berechnungen wirken sich die klimaschutzbedingten Zusatzkosten für die Stahl-, Zement- und HVC-Produktion nur marginal auf die Herstellungskosten der Endprodukte (z. B. Pkw, Gebäude, Medikamente) aus. Allerdings basiert die verwendete Modellierung auf starken Vereinfachungen, sodass komplexere Modelle und eine bessere sowie aktuelle Datenbasis notwendig sind, um Kosten- und Preiseffekte genauer abschätzen zu können. Dies würde es auch ermöglichen, ggf. nötige staatliche Kompensationsmechanismen für klimaschutzbedingte Mehrkosten an den tatsächlichen Bedarfen auszurichten.
Wie lassen sich die Risiken für Produktionsverlagerungen effektiv mindern?
Die Verlagerung von Teilen der Grundstoffproduktion in Weltregionen mit geringerer CO2-Kostenbelastung (Carbon Leakage) oder mit besseren Bedingungen für die Erzeugung von erneuerbaren Energien (Green Leakage) stellt eine relevante Gefahr für den Wirtschaftsstandort Deutschland bzw. Europa dar. Zur Minderung der Risiken existieren verschiedene politische Instrumente. Welche Instrumente bzw. Instrumentenbündel (ggf. in welcher zeitlichen Abfolge) den effektivsten Schutz vor Carbon bzw. Green Leakage bieten, ist eine noch offene Frage. Um sie zu beantworten, ist ein besseres Verständnis der Ursachen und Folgen von Carbon bzw. Green Leakage notwendig. Forschungsbedarf besteht u. a. zu folgenden Aspekten:
- Welche Grundstoffindustrien (und ggf. nachgelagerte Wertschöpfungsstufen) sind besonders durch Carbon oder Green Leakage gefährdet und welche ökonomischen Ausmaße könnten diese Effekte annehmen?
- Wie beeinflussen unterschiedlich plausible Annahmen zum Verhalten bzw. zur Klimaschutzpolitik anderer Weltregionen die Investitionsentscheidungen in den Unternehmen der Grundstoffindustrie? Welche Rolle spielen hierbei aktuelle politische Beschlüsse und Diskussionen?
- Ist das CO2-Grenzausgleichssystem in seiner aktuellen Ausgestaltung geeignet, um den schrittweisen Ausstieg der kostenlosen Zuteilung von Emissionszertifikaten ohne Gefahren für Carbon Leakage zu vollziehen? Wie müsste das System ggf. weiterentwickelt werden?
- Inwieweit ist es aus gesamtwirtschaftlicher Sicht überhaupt sinnvoll, Green Leakage zu vermeiden bzw. zu begrenzen? Wäre es ggf. klüger, grüne Grundstoffe künftig in größeren Mengen zu importieren, um den Fokus der heimischen industriellen Produktion stärker auf die Weiterverarbeitung zu innovativen und hochqualitativen Produkten zu legen?
Arbeitsplatzeffekte der Transformation besser verstehen
Infolge der erwarteten (moderaten) Produktionsrückgänge sowie einer höheren Prozessautomatisierung sind in den untersuchten Grundstoffindustrien gewisse Arbeitsplatzverluste nicht auszuschließen. Ob diese Verluste durch ebenfalls absehbare gegenläufige Effekte (z. B. durch zusätzliche Arbeitsschritte beim Einsatz der CO2-Abscheidung) kompensiert werden können, ist nach derzeitigem Kenntnisstand jedoch kaum abzuschätzen. In den vor- und nachgelagerten Wertschöpfungsketten scheinen hingegen deutlich die positiven Arbeitsplatzeffekte zu überwiegen (z. B. infolge des nötigen Aufbaus einer Wasserstoffwirtschaft), allerdings lassen sich die Effekte auch hier noch nicht genau quantifizieren.
Um mit zielgerichteten arbeits- und bildungspolitischen Maßnahmen die Transformation so sozialverträglich wie möglich zu gestalten, ist ein besseres Verständnis der zu erwartenden Arbeitsplatzeffekte einschließlich der Auswirkungen auf die Qualifikationsanforderungen für die Beschäftigten notwendig. Dazu könnten u. a. folgende Forschungsaktivitäten beitragen:
- Weiterentwicklung der makroökonomischen Modellierung zu gesamtwirtschaftlichen Effekten der Transformation (Wertschöpfung, Arbeitsplatzeffekte) für unterschiedliche Annahmen zu den zukünftigen Produktionsmengen in Deutschland;
- regionalwirtschaftliche Untersuchungen der möglichen sozioökonomischen Auswirkungen für spezielle Regionen bzw. industrieller Cluster;
- Untersuchungen zu den zukünftigen Qualifikationsanforderungen einer klimaneutralen Grundstoffproduktion: Wie werden sich die Anforderungen im Zeitverlauf verändern? Inwieweit und mit welchen Fortbildungen können Beschäftigte mit bisherigen und zukünftig nicht mehr (in gleichem Umfang) benötigten Qualifikationen umgeschult werden?
5.3 Ausblick
Ziel des TA-Projekts war die Analyse und Bewertung der Realisierungsbedingungen für eine (weitgehende) Klimaneutralität bis 2045 der drei emissionsintensivsten Grundstoffindustrien Eisen/Stahl, Zement und HVC. Die Ergebnisse dieser breiten und komplexen Untersuchung zeigen, dass die Transformation technisch machbar erscheint, obgleich eine Reihe an technologischen und politischen Herausforderungen gemeistert werden müssen. Um die Transformation erfolgreich umzusetzen, erscheint insbesondere ein integratives Gesamtkonzept wichtig, das über den Gegenstand der Untersuchung hinaus wichtige Konzepte der Nachhaltigkeit, wie etwa die Materialeffizienz und -suffizienz in Industrie und Gesellschaft, nicht ausklammert.
Abbildungen
- Abb. 2.1 Ausgewählte alternative Routen der Stahlproduktion mit Prozessschritten und Zwischenprodukten
- Abb. 2.2 Routen der Zementproduktion mit Prozessschritten und Zwischenprodukten (vereinfachte Darstellung)
- Abb. 2.3 Routen der HVC-Produktion (vereinfachte Darstellung)
- Abb. 3.1 Produktionskosten Stahl (in Euro t/Rohstahl)
- Abb. 3.2 Entwicklungspfad B: Hüttensandbedarf und -verfügbarkeit
- Abb. 3.3 Spezifische Kosten der Zementherstellung
- Abb. 3.4 Spezifische Kosten HVC-Produktion
Fußnoten
1 BVerfG, Urteil des Zweiten Senats vom 15.11.2023 - 2 BvF 1/22 -, Rn. 1-231
2 Zweites Nachtragshaushaltsgesetz 2021 vom 18.2.2022
3 direktreduziertes Eisen (Direct Reduced Iron – DRI)
GU Prognos/Wuppertal Institut 2022
4 Weil im Rahmen des TA-Projekts keine Gesamtsystemberechnungen möglich waren, wurden mögliche Entwicklungen der übrigen Branchen und Sektoren aus externen Szenariostudien abgeleitet.
5 Eine Ausnahme hiervon wurde für Zement gemacht: Hier schreitet die Substitution der günstigen Braunkohle durch Erdgas schneller voran als die Substitution der fossilen durch erneuerbare Energieträger. Dies führt zwischenzeitlich zu einem steigenden Erdgasbedarf, der in absoluten Mengen allerdings gering ist.
6 Der Endenergiebedarf für die wasserstoffbasierte Direktreduktion bezieht sich auf den Energieinhalt des Wasserstoffs. Wird der Bedarf an erneuerbarem Strom für die Elektrolyse mitgerechnet, relativiert sich der energetische Vorteil.
7 In dieser Analyse stand der direkte Energiebedarf, den die deutschen HVC-Hersteller aufwenden müssen, im Fokus. Der Energiebedarf für die vorgelagerte Rohstoffherstellung (externer Bezug) wurde dementsprechend nicht berücksichtigt. In Bezug auf Stoffströme und Kosten sind die Rohstoffe (durch Ausweisung als externer Bezug mit einem entsprechenden Preis) jedoch vollständig abgebildet.
8 Die Investitionsimpulse der beiden Pfade wurden gemittelt, da sich die jeweiligen Investitionsvolumina in der Summe nicht wesentlich unterscheiden.
9 Wachstumschancengesetz vom 27.3.2024
10 Durch das Urteil des Bundesverfassungsgerichts vom 15.11.2023 zum Zweiten Nachtragshaushaltsgesetz 2021 ist die Finanzierung von entsprechenden Förderprogrammen derzeit teilweise unsicher. Die Folgen des Urteils für die weitere politische Unterstützung der Transformation der Grundstoffindustrien können an dieser Stelle aber nicht antizipiert werden.
11 Eine Abschätzung von Importquoten für grüne Ressourcen war im Rahmen dieses TA-Projekts nicht möglich, da keine Gesamtsystemberechnungen vorgenommen wurden.
12 Dieses Thema wird vom TAB aktuell im TA-Projekt »Chancen und Risiken von Wasserstoffpartnerschaften und -technologien in Entwicklungsländern« bearbeitet.
13 Kohlendioxid-Speicherungsgesetz vom 17.8.2012, zuletzt am 10.8.2021 geändert
14 Energiewirtschaftsgesetz vom 7.7.2005, zuletzt am 22.12.2023 geändert
Im Bundestag
- Vorgang - Bericht, Gutachten, Programm im Dokumentations- und Informationssystem für Parlamentsmaterialien (DIP)
In den Medien
- riffreporter.de (24.06.2024), TAB-Bericht: So können Stahl, Zement und Grundchemikalien in Deutschland klimaneutral werden.
- tech2go.podigee.io (05.06.2024) Podcast Weekly #61: Kosten für klimafreundliche Industrie, Roboterfußball und eine Ratte erklärt die Menschheit.
- t3n.de (29.05.2024), Prognosen für klimafreundlicheren Stahl und Zement: Erst teurer, dann günstiger.
- spektrum.de (+) (28.05.2024), Stahl, Zement, Chemikalien: Was kostet eine klimaneutrale Industrie?
- tagesspiegel.de (+) (28.05.2024), Erst teurer, dann günstiger: Wie Stahl, Zement und Chemie klimaneutral werden könnten.
- sciencemediacenter.de (28.05.2023), Klimaneutrale Herstellung von Stahl, Zement und Grundchemikalien. Fünf Expertenstatements zur Einordnung des TAB-Berichts.